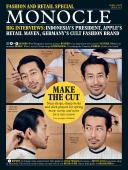
Issue 112
Fashion and retail special. Big interviews: Indonesia’s president, Apple’s retail maven and Germany’s cult fashion brand.
In This Issue
Oops! No content was found.
Looks like we no longer have content for the page you're on. Perhaps try a search?
Return Home