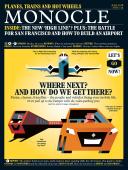
Issue 114
Where next? And how do we get there? Faster, cleaner, friendlier – the people and vehicles fixing your mobile life. Plus: pull up to the bumper with valet-parking pros.
In This Issue
Oops! No content was found.
Looks like we no longer have content for the page you're on. Perhaps try a search?
Return Home