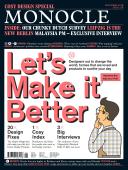
Issue 118
Let’s make it better: improve the way you live. Designers out to change the world, homes that are loved and products to soothe your day.
In This Issue
Oops! No content was found.
Looks like we no longer have content for the page you're on. Perhaps try a search?
Return Home