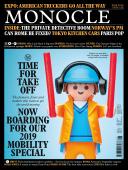
Issue 124
Time for take off! The pioneers, fixers and makers who want to get the world moving.
In This Issue
Oops! No content was found.
Looks like we no longer have content for the page you're on. Perhaps try a search?
Return HomeClick here to discover more from Monocle
Time for take off! The pioneers, fixers and makers who want to get the world moving.
Looks like we no longer have content for the page you're on. Perhaps try a search?
Return Home