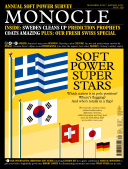
Issue 139
As we prepare to ring in 2021, it’s time to look back and assess which countries are flying high in our annual Soft Power Survey. There’s plenty to take stock of in Monocle’s end-of-year December/January issue: from a range of voices on what’s next for the US, to the power of rural reinvention and the big business of looking forward. We’ve got all your holiday prepping sorted, too, with an inspiring 15-page gift guide – and an extensive run-down of all the books, TV shows and films that will keep you stimulated this winter.
In This Issue
Oops! No content was found.
Looks like we no longer have content for the page you're on. Perhaps try a search?
Return Home