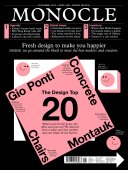
Issue 148
The perfectly formed November issue of Monocle is a design special that puts the brands, architects and products you need to know in the frame. We also visit a Gio Ponti masterwork in Paris and discuss the merits of concrete and its impact on the environment. Plus: bangers in Berlin and why Lisbon is the new Leblon.
In This Issue
Oops! No content was found.
Looks like we no longer have content for the page you're on. Perhaps try a search?
Return Home