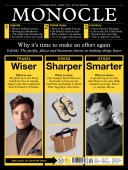
Issue 157
Monocle’s October issue is all about making an effort, whether that’s designing a distinctive uniform for your business, decking out your apartment so that hosting is easy or sharpening up your autumn style. We cover it all. Plus: Will Brazil stick or twist as election day nears?
In This Issue
Oops! No content was found.
Looks like we no longer have content for the page you're on. Perhaps try a search?
Return Home