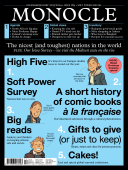
Issue 169
Monocle’s bumper December/January double issue surveys the world’s most influential nations, from the European country with visa-free travel to 190 states to the Asian outpost with a crooning president. Elsewhere, we reveal the history of French animated storytelling with a comic of our own and plot a course for a fruitful festive shopping spree in a city near you.
In This Issue
Oops! No content was found.
Looks like we no longer have content for the page you're on. Perhaps try a search?
Return Home