In This Issue
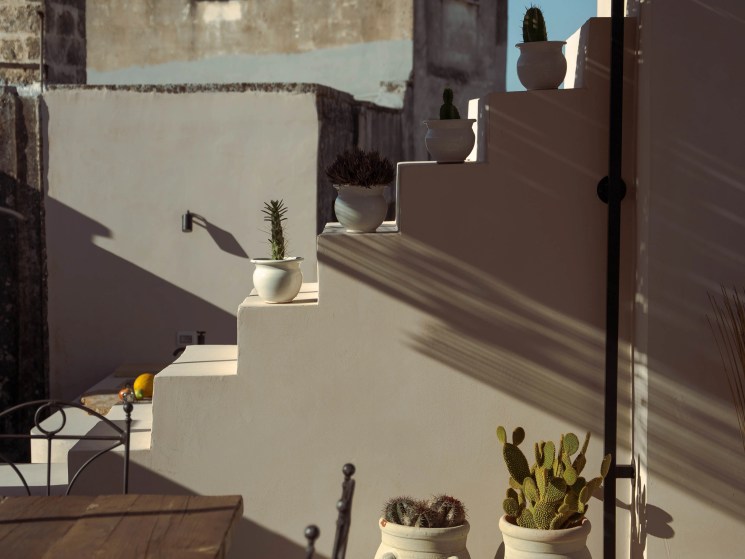
- 174 | Issues
- 5 min read
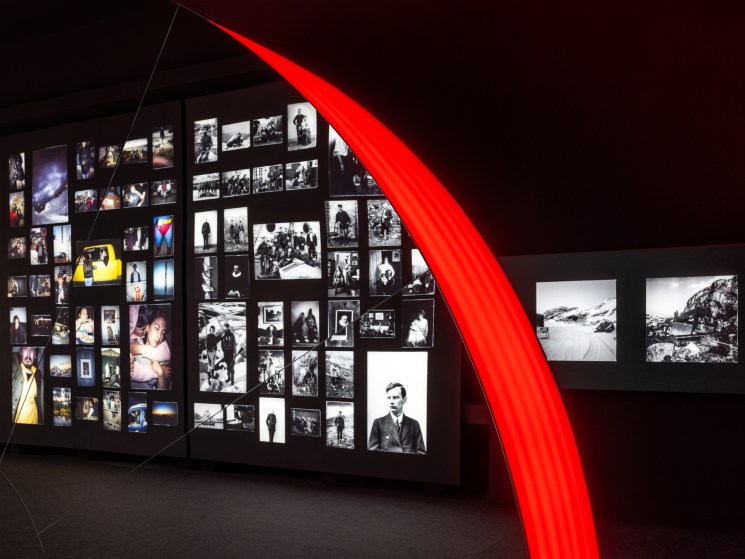
- 174 | Issues
- 7 min read
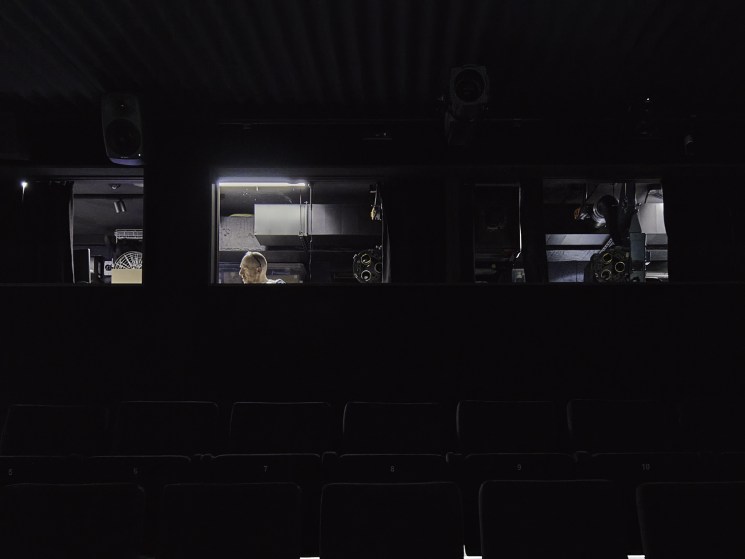
- 174 | Issues
- 6 min read
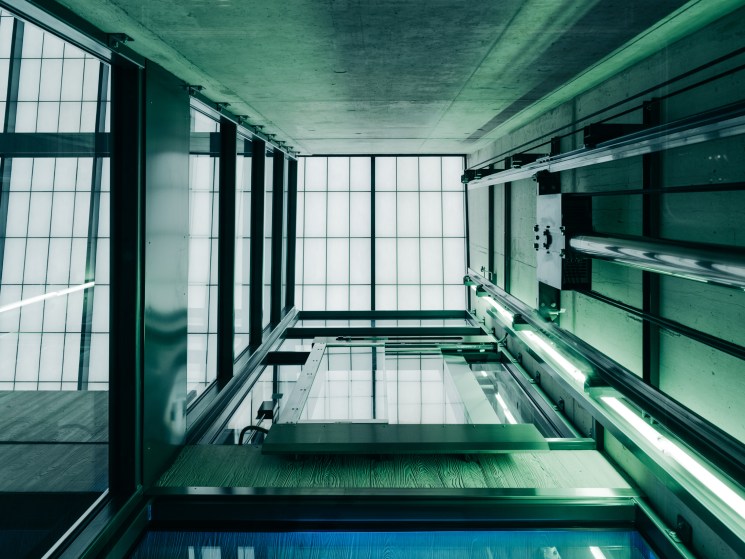
- 174 | Issues
- 9 min read

- 174 | Issues
- 3 min read
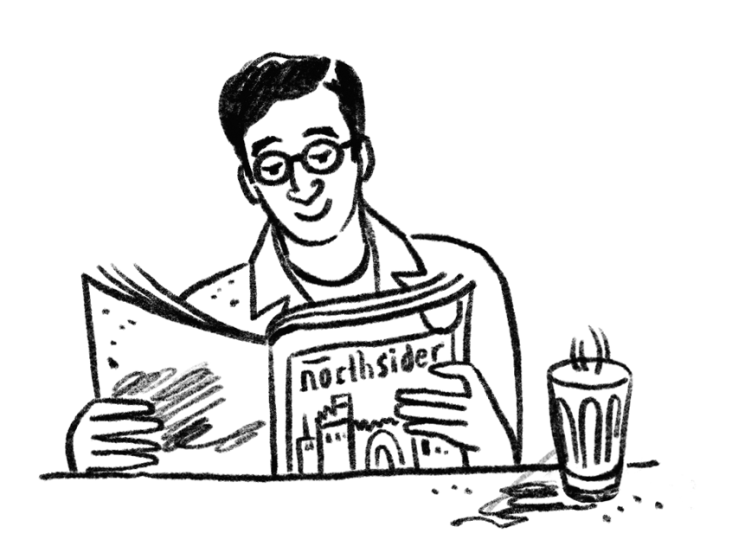
- 174 | Issues
- 5 min read
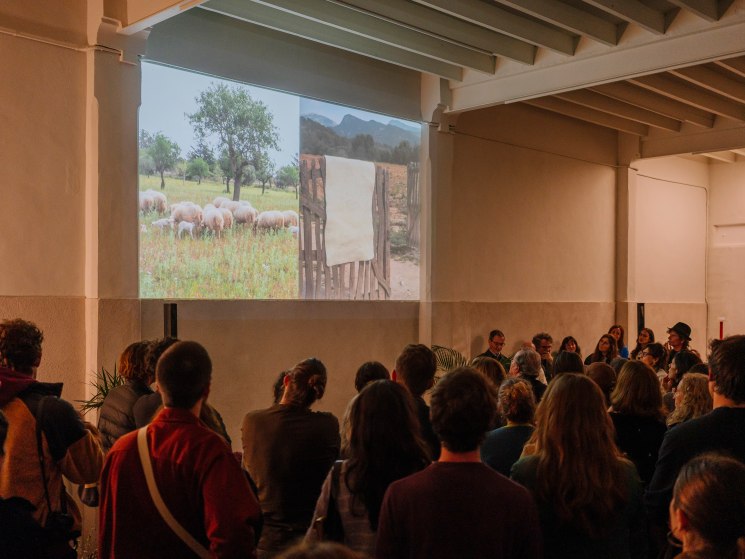
- 174 | Issues
- 11 min read
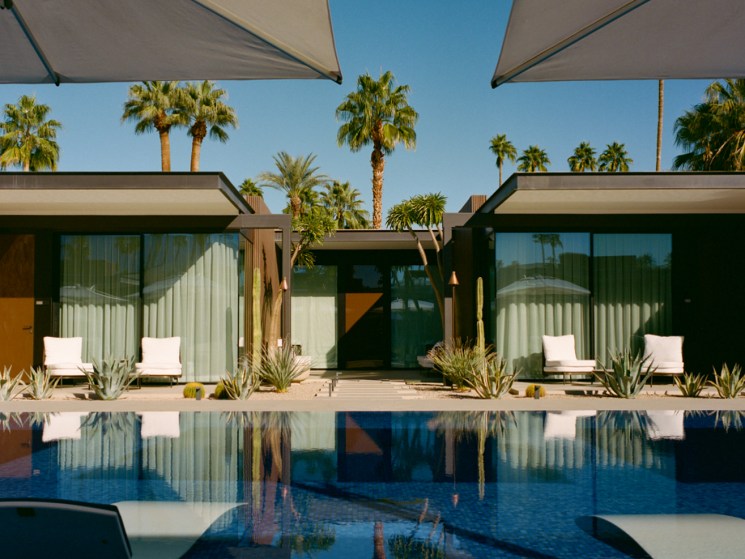
- 174 | Issues
- 11 min read
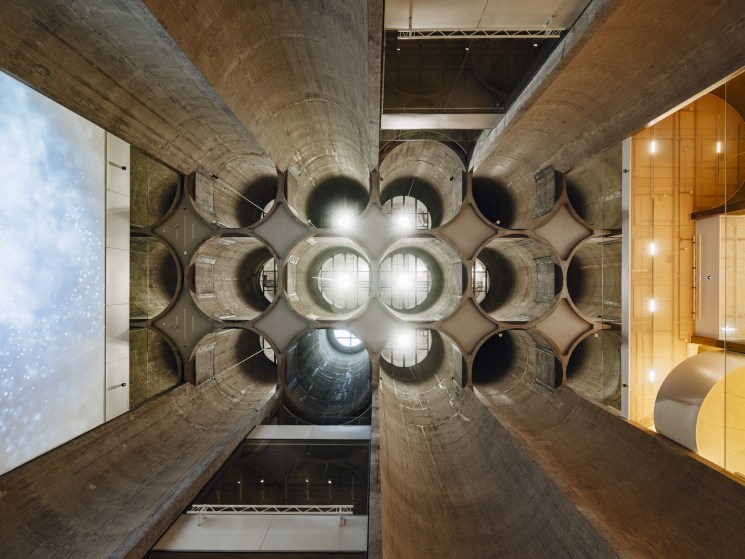
- 174 | Issues
- 22 min read

- 174 | Issues
- 6 min read
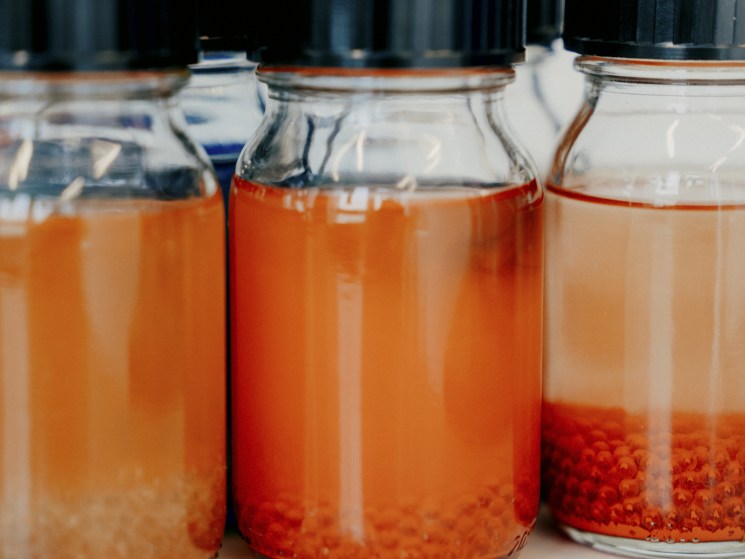
- 174 | Issues
- 11 min read

- 174 | Issues
- 15 min read