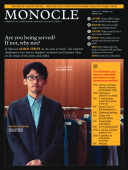
Issue 22
Are you being served? If not, why not? A Monocle global survey on the state of retail – the smartest shopkeepers, best buyers, happiest customers and sharpest ideas on the street, in the aisles and online.
In This Issue
Oops! No content was found.
Looks like we no longer have content for the page you're on. Perhaps try a search?
Return Home