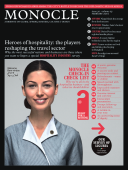
Issue 30
Why the most successful nations and businesses are those where you want to linger: a special hospitality industry survey.
In This Issue
Oops! No content was found.
Looks like we no longer have content for the page you're on. Perhaps try a search?
Return Home