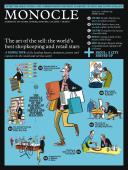
Issue 32
Monocle’s April issue looks at the art of the sell with a global tour of the leading buyers, designers, cutters and curators in the retail sector. We also bring you our in-depth guide to Seoul in our city survey.
In This Issue
Oops! No content was found.
Looks like we no longer have content for the page you're on. Perhaps try a search?
Return Home