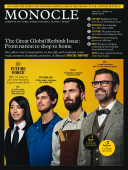
Issue 42
Monocle’s new edition is our Global Rethink issue, where we focus on the businesses and sectors that are making a trip back to the drawing board.
In This Issue
Oops! No content was found.
Looks like we no longer have content for the page you're on. Perhaps try a search?
Return Home