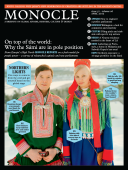
Issue 52
From Europe’s High North Monocle reports on a fresh model for people power – a survey of relaunched capitals and new parliaments.
In This Issue
Oops! No content was found.
Looks like we no longer have content for the page you're on. Perhaps try a search?
Return Home