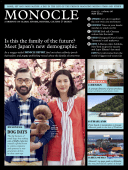
Issue 53
In issue 53 you’ll find a report on the supersized doggy pampering industry in Japan, our Affairs lead on Brazil’s command of the UN peace-keeping mission in Haiti, and special supplements including the Design Directory for 2012.
In This Issue
Oops! No content was found.
Looks like we no longer have content for the page you're on. Perhaps try a search?
Return Home