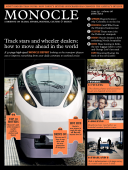
Issue 54
In issue 54 of Monocle we climb aboard for the 2012 Transport Survey, head to Dallas to learn how it’s becoming an art destination and also look at the companies making the upcoming London Olympics a reality.
In This Issue
Oops! No content was found.
Looks like we no longer have content for the page you're on. Perhaps try a search?
Return Home