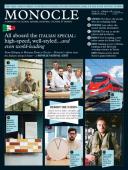
Issue 71
All aboard the Italian special: high-speed, well-styled… and even world-leading. From Bologna to Bolzano, Turin to Treviso — Monocle’s editors meet the Italians doing it better — a Monocle National Audit.
In This Issue
Oops! No content was found.
Looks like we no longer have content for the page you're on. Perhaps try a search?
Return Home