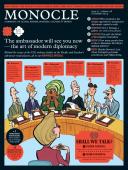
Issue 77
The ambassador will see you now — the art of modern diplomacy. Behind the scenes at the UN, embassy battles in the Pacific and Sweden’s soft-power retail players, all in our Monocle Special
In This Issue
Oops! No content was found.
Looks like we no longer have content for the page you're on. Perhaps try a search?
Return Home