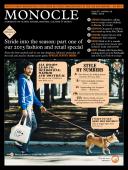
Issue 82
Stride into the season: part one of our 2015 fashion and retail special. From the best-stocked rails to our top designers, Monocle unleashes all the tools you need to sharpen your game: Special Survey Series
In This Issue
Oops! No content was found.
Looks like we no longer have content for the page you're on. Perhaps try a search?
Return Home