Expo / Global
In good hands
For Europe’s storied luxury brands, the future depends on safeguarding the traditions of the past. That’s why dedicated schools across the continent are working to ensure that younger generations learn the traditional crafts that we can’t afford to lose.
The rise of AI and a slowdown in luxury consumption have cast a shadow over the fashion and design sectors. Yet heritage luxury businesses are taking a longer-term view. Instead of following technological trends or being discouraged by market conditions, they’re doubling down on the crafts that they have honed for decades – or even centuries.
Forward-looking brands are making significant investments in education, hoping to pass down craft skills to younger generations – not only through apprenticeship schemes but by opening dedicated schools where veteran artisans are given the time and space to train the masters of the future. Here, monocle visits some of the most prominent of these institutions – from Ligne Roset’s École de Formation outside Lyon, where students learn about upholstery, to Brioni’s Scuola di Alta Sartoria Nazareno Fonticoli in Abruzzo, where tailor Angelo Petrucci instructs young people in the fine art of making the perfect cut. These classrooms are focused on the transmission of knowledge but they’re also creating opportunities for intergenerational conversations, while helping to turn craft into an attractive career path for new cohorts. And they offer a peek at the future of luxury, which remains defined by the human touch. —
1.
tailoring
Brioni
Scuola di Alta Sartoria Nazareno Fonticoli, Italy
Brioni has championed the art of tailoring since 1945, when Nazareno Fonticoli founded the label in Rome. After noticing a decline in uptake for artisanal roles in the 1980s, the label took action, establishing the Scuola di Alta Sartoria Nazareno Fonticoli in the city of Penne. “Back then, we had a problem with the new generation taking up the craft because the process of making any money from it is long,” says Angelo Petrucci, Brioni’s chief master tailor and head of product design. “But for almost 40 years, the school has been transforming young people into custodians of noble traditions.”
The school’s 16 professors teach classes on subjects ranging from pattern design to textiles. Students are typically aged between 23 and 28; to become one of them, applicants must complete a practical stitching test. However, the most important attributes are enthusiasm and motivation, says Emidio Fonticoli, a member of the Brioni founder’s family and Fondazione Brioni’s president. Fonticoli, who is also the school’s director, welcomes monocle to the newly renovated institution that comprises several classrooms with views of the Abruzzi landscape. Inside, students are taught to perfect the 220 steps required to finish a Brioni suit, which are all executed manually. “The machine is a support tool and not a substitute for the hand of the artisan,” says Petrucci.
On the day of monocle’s visit, the students are in the middle of an English lesson (Italian lessons are also provided for international students). It’s one of several extracurricular activities that have turned the school into an increasingly sought-after destination for students.
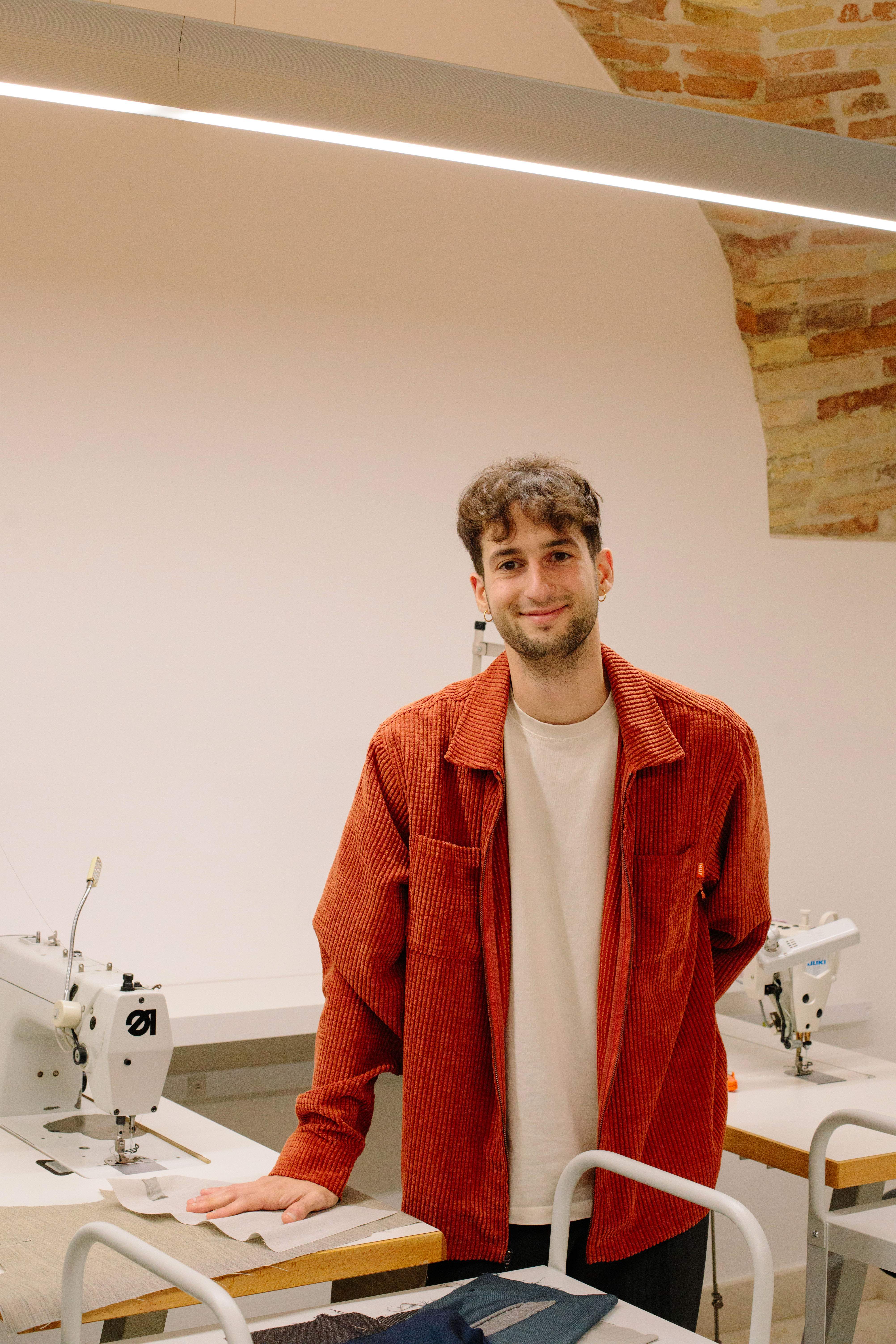
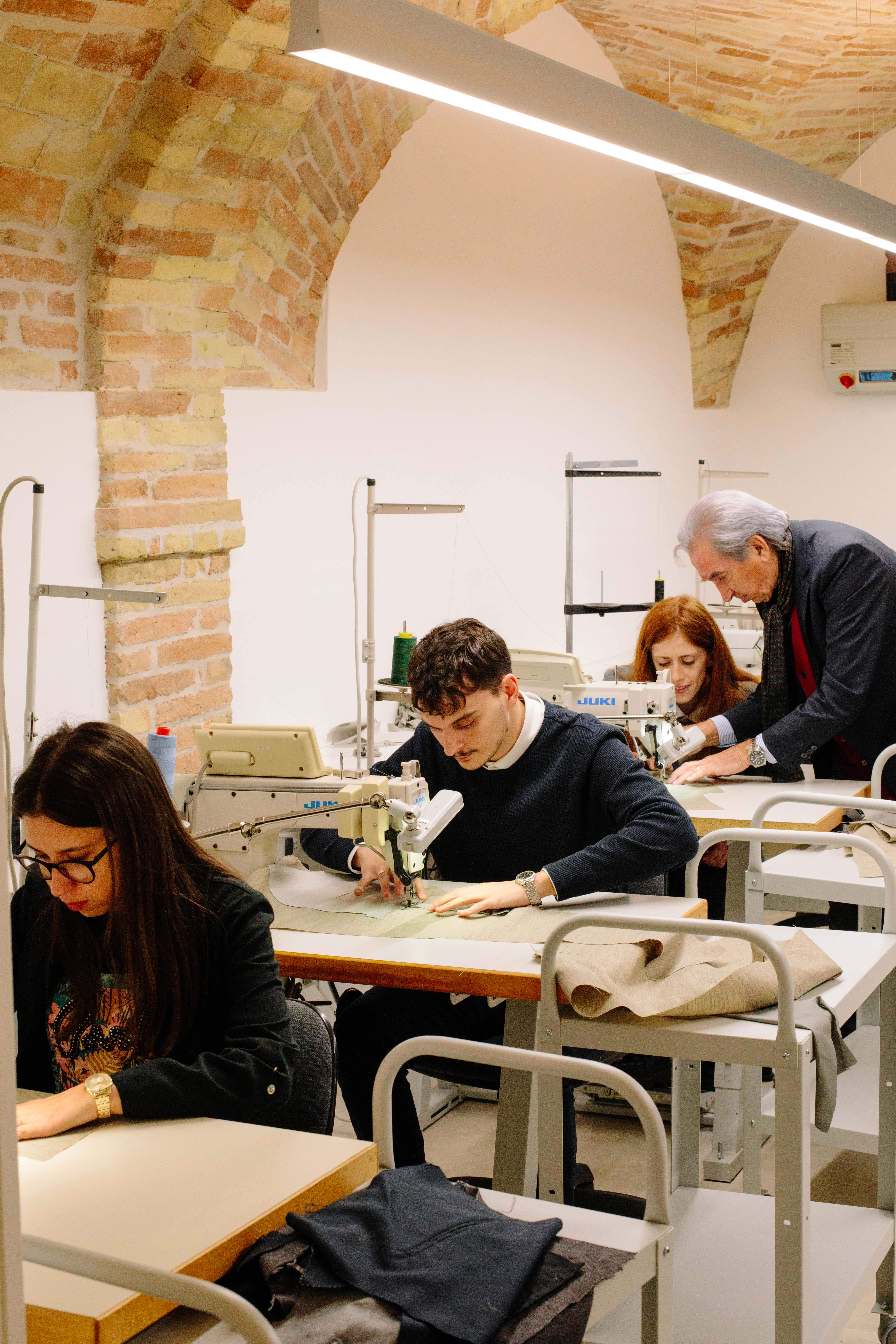
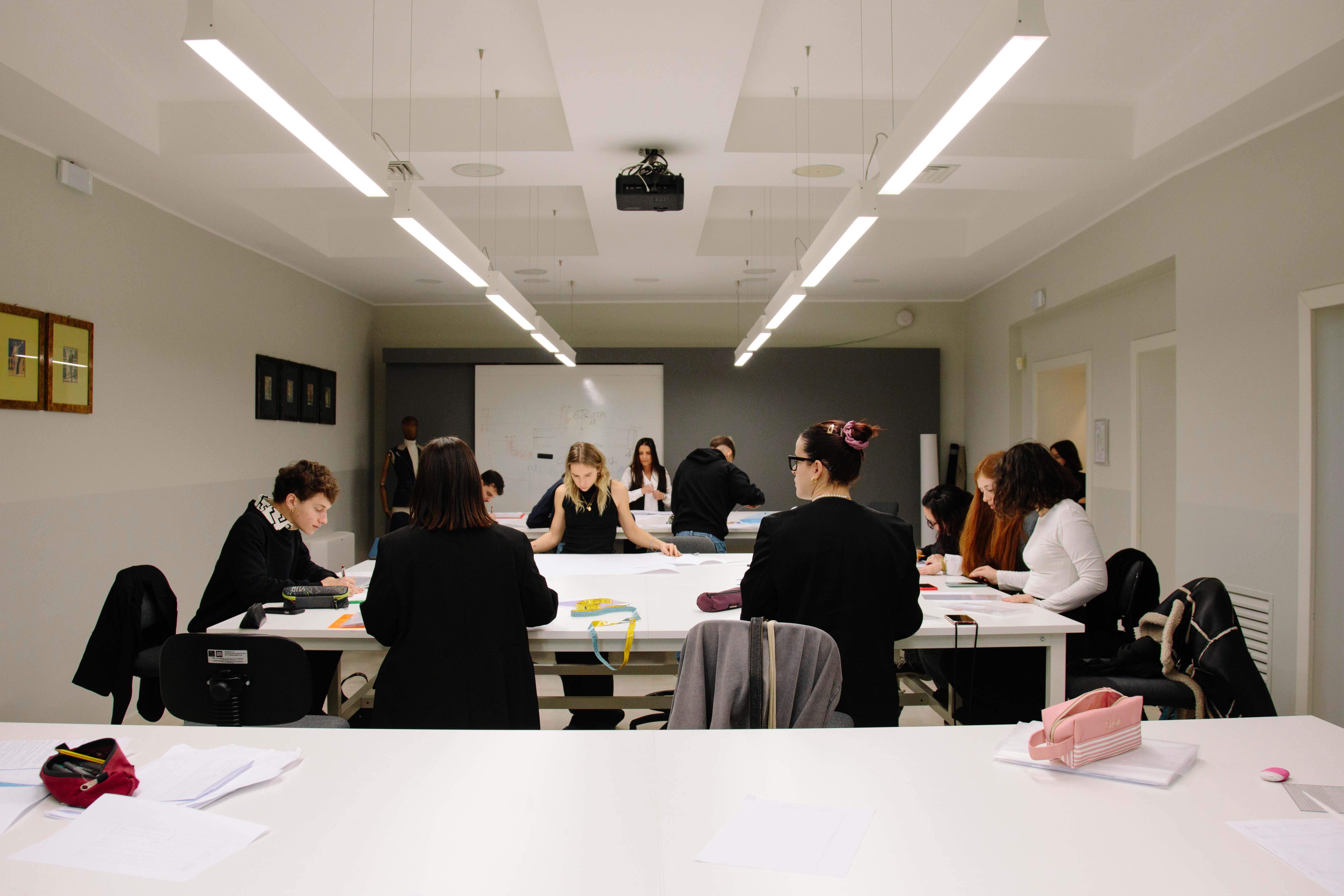
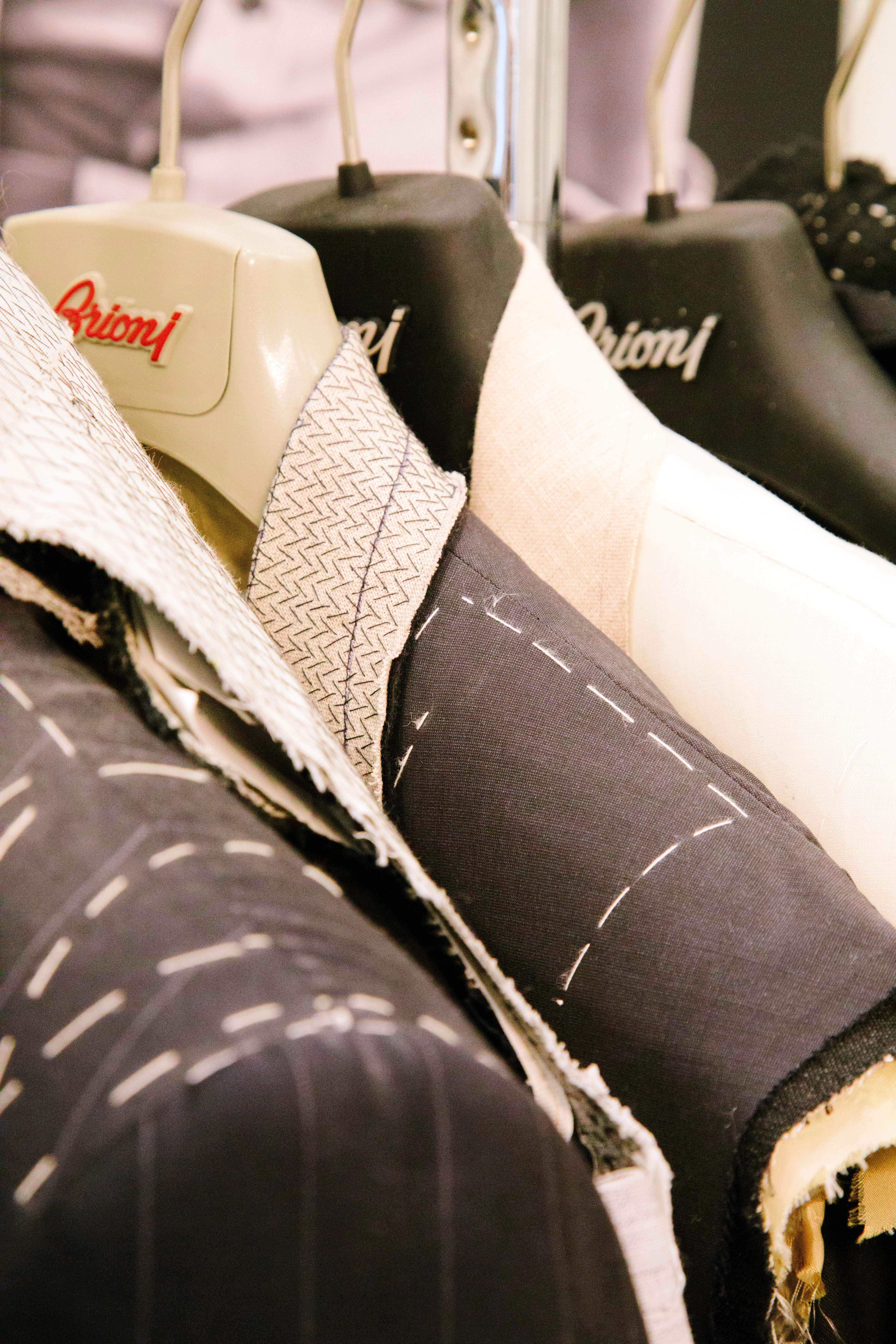
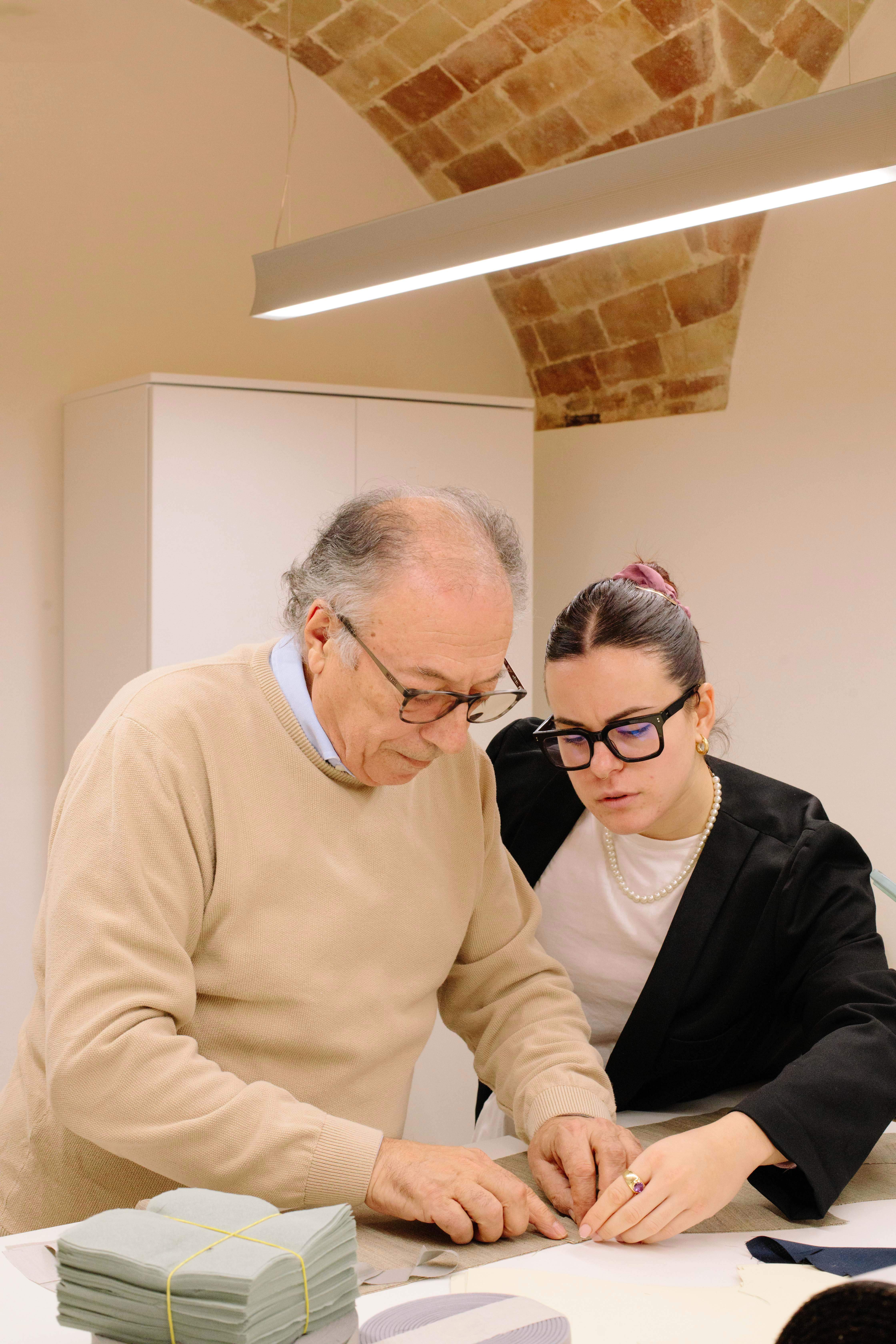
2.
upholstery
Ligne Roset
École de Formation, France
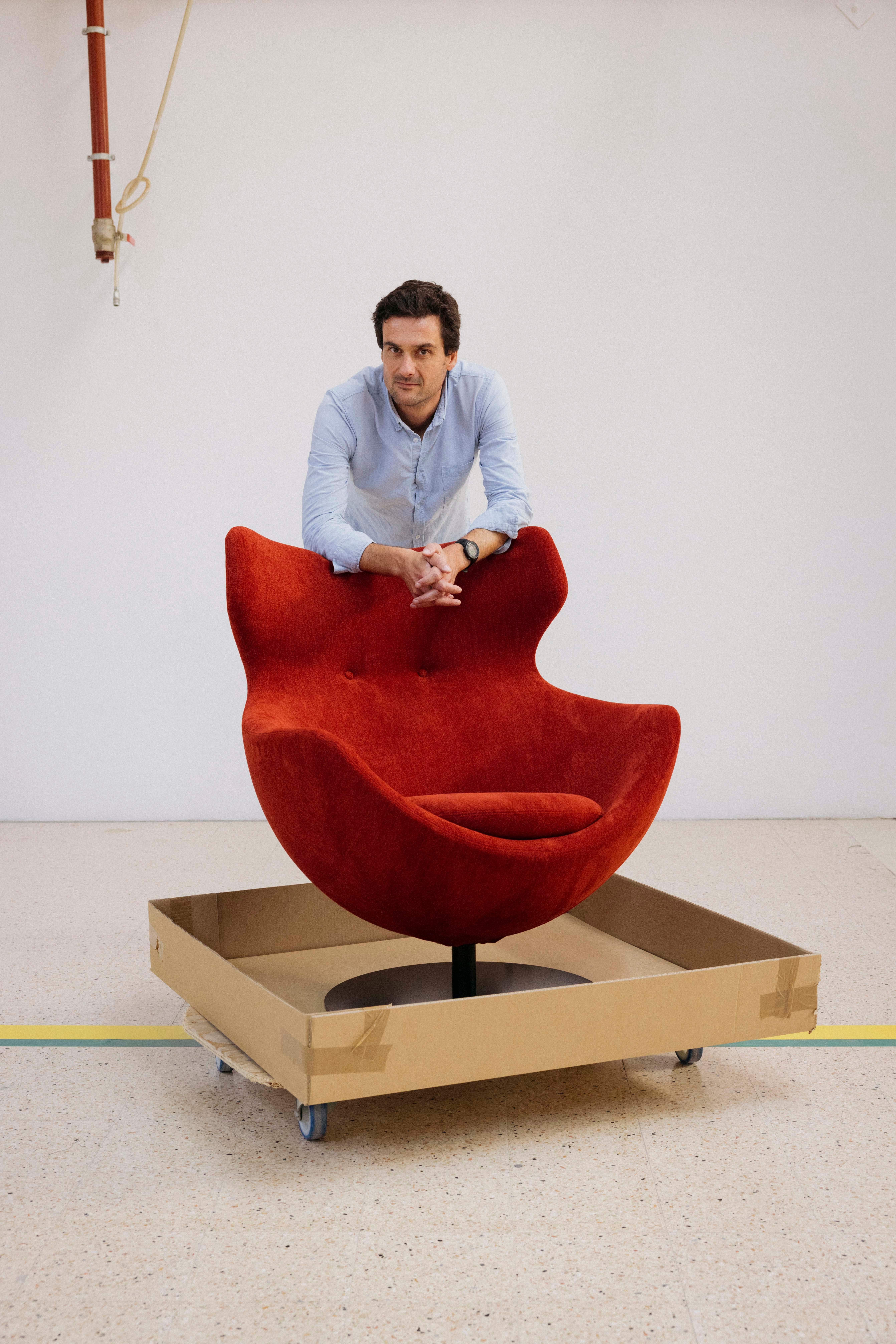
At Ligne Roset, the transmission of craft skills had always been part of an organic mentorship process between generations of artisans, known as compagnonage. But in 2020 the brand, which is based in the small town of Briord, decided to formalise it. “The coronavirus pandemic highlighted the risk of staff shortages, especially when the generation that had been working here for 40 years suddenly retired all at once,” says co-ceo Olivier Roset. As a result, he decided to open the École de Formation, in partnership with the Auvergne-Rhône-Alpes regional government. The school offers training in upholstery and furniture sewing.
The 160-year-old brand has long required its workers to hone specific upholstery skills but these have traditionally been taught on the factory floor. “Unlike for fashion sewing, there aren’t schools that teach what we do,” says Roset. “By investing in training, we are ensuring our longevity.”
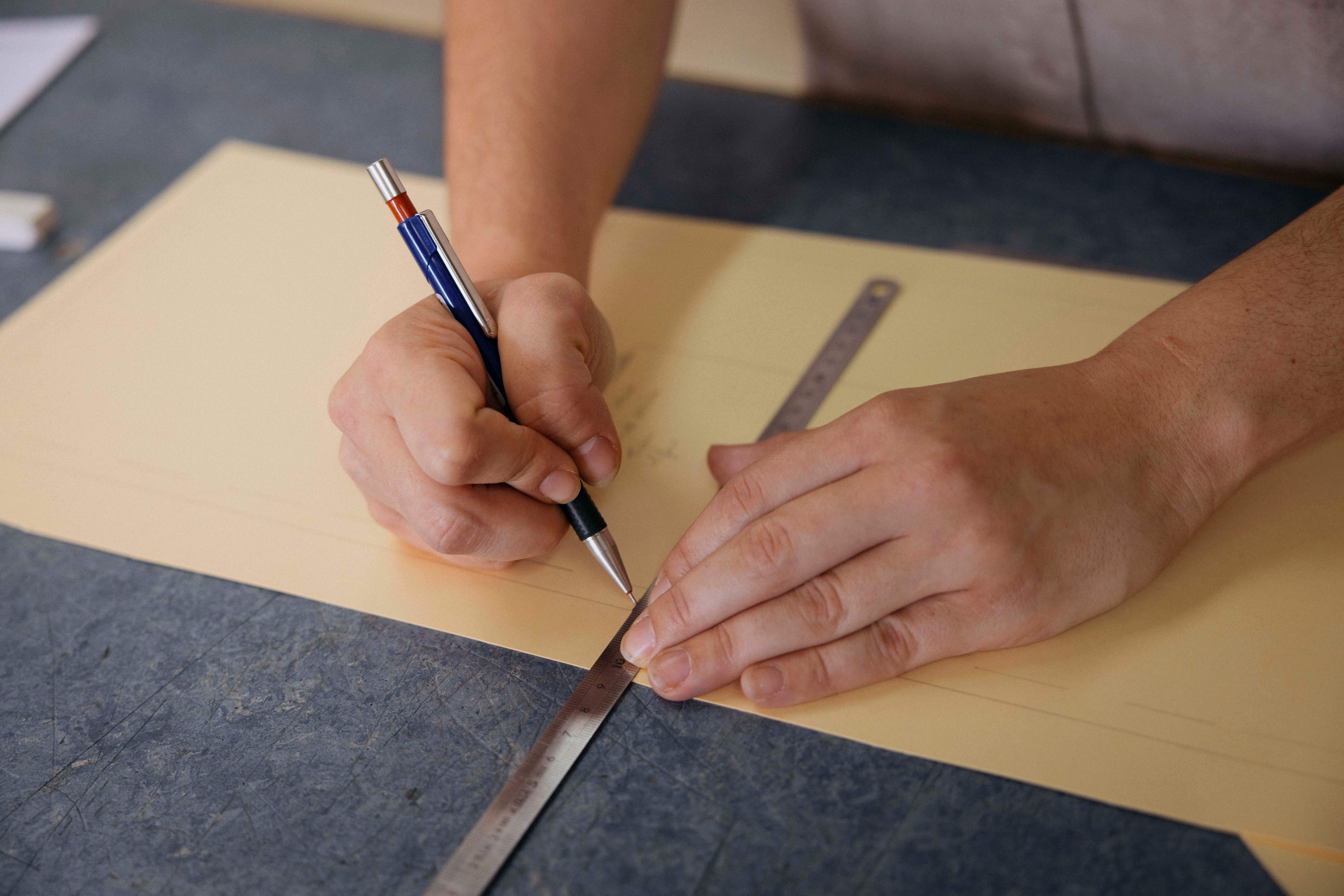
The school’s 600-hour course is divided between classic and contemporary upholstery, and also teaches specialised Ligne Roset techniques. The students will soon move to a dedicated building on the brand’s campus, featuring classrooms and an atelier.
“The renovations allow us to create an ecosystem where we can train young starters but also long-time employees looking to evolve their career,” says Roset. Investing in education allows the company to offer new opportunities to employees, who can then become teachers. “The best are those who know how to pass on their skills and passion with patience,” he adds. “We want to encourage these intergenerational connections.”
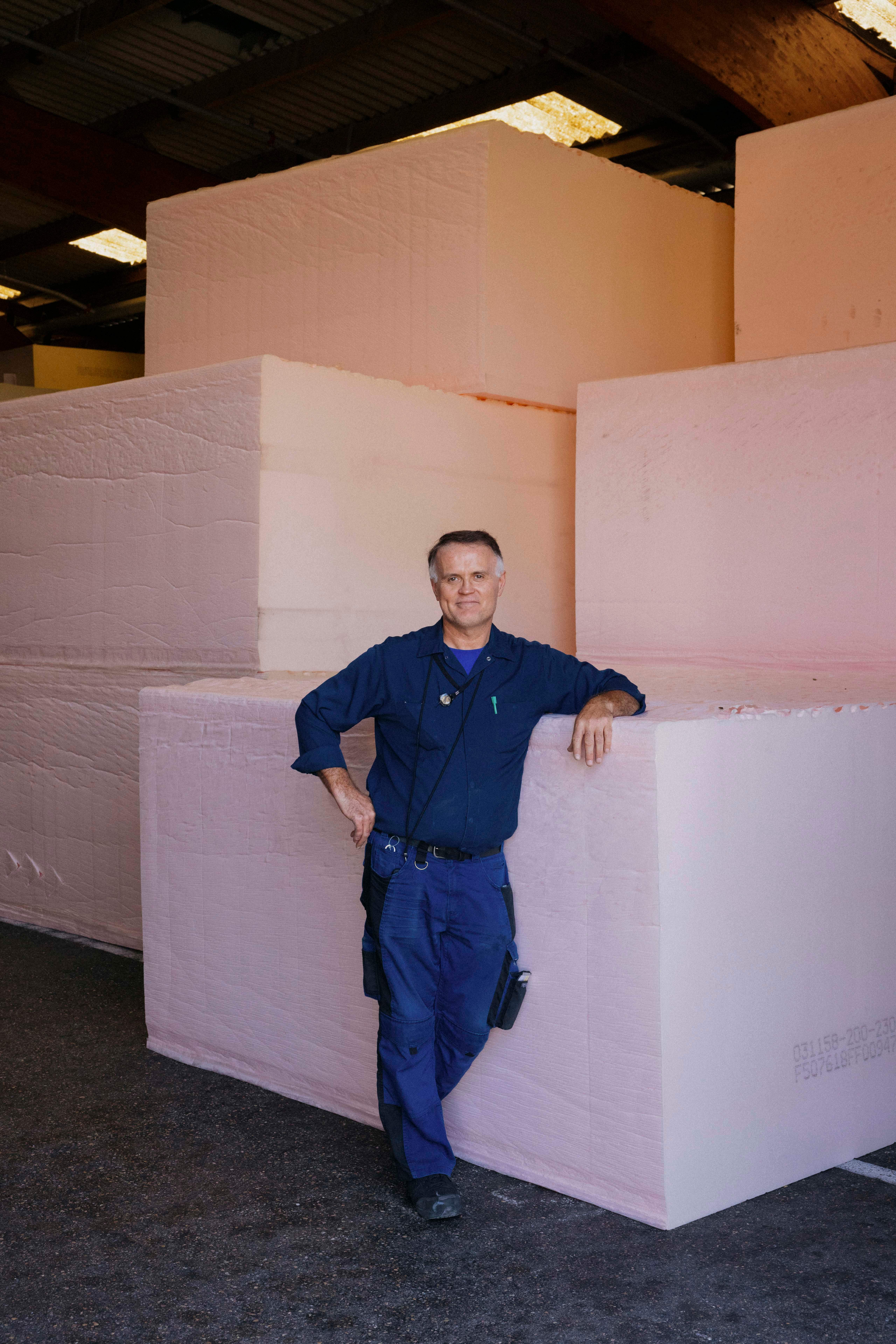
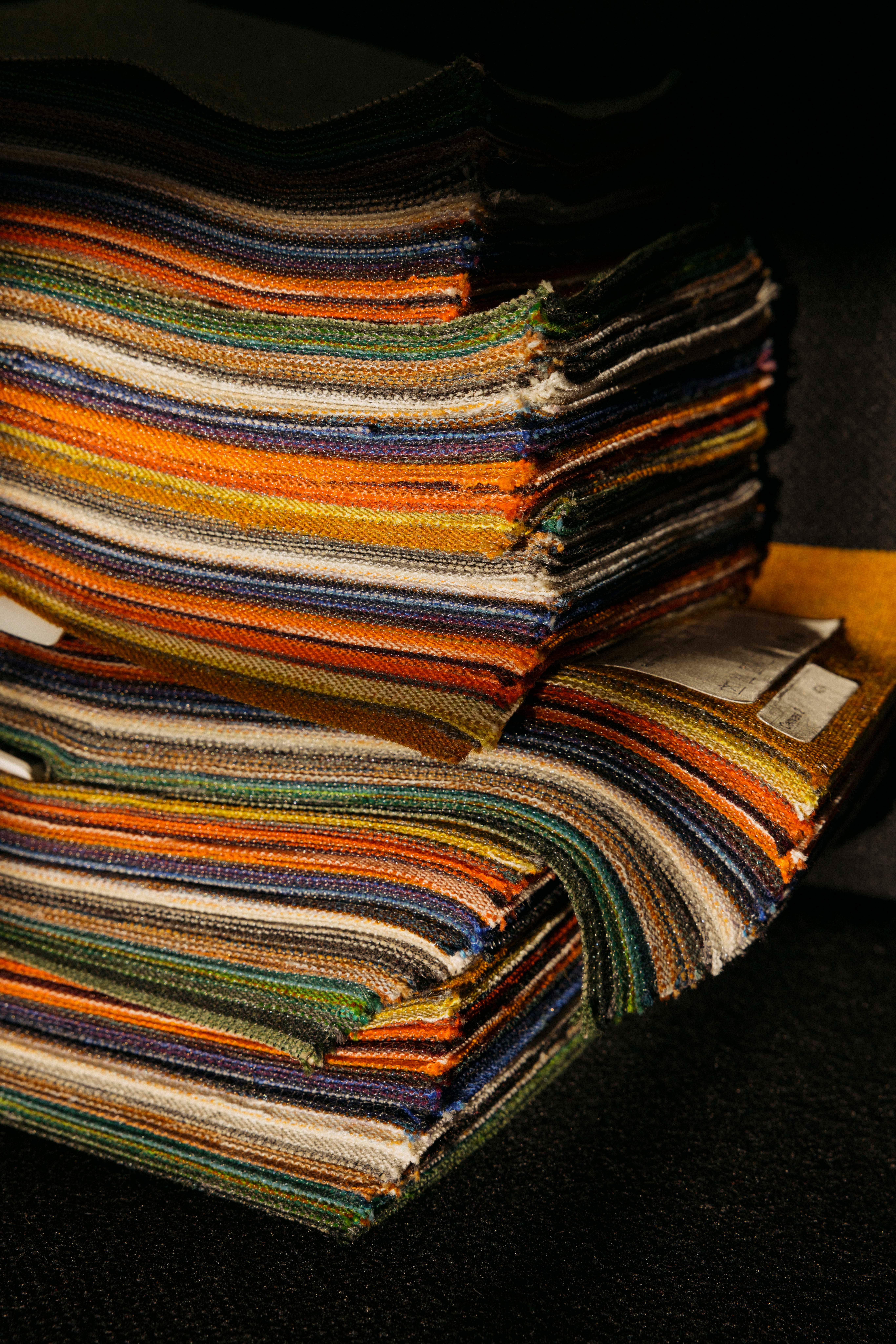
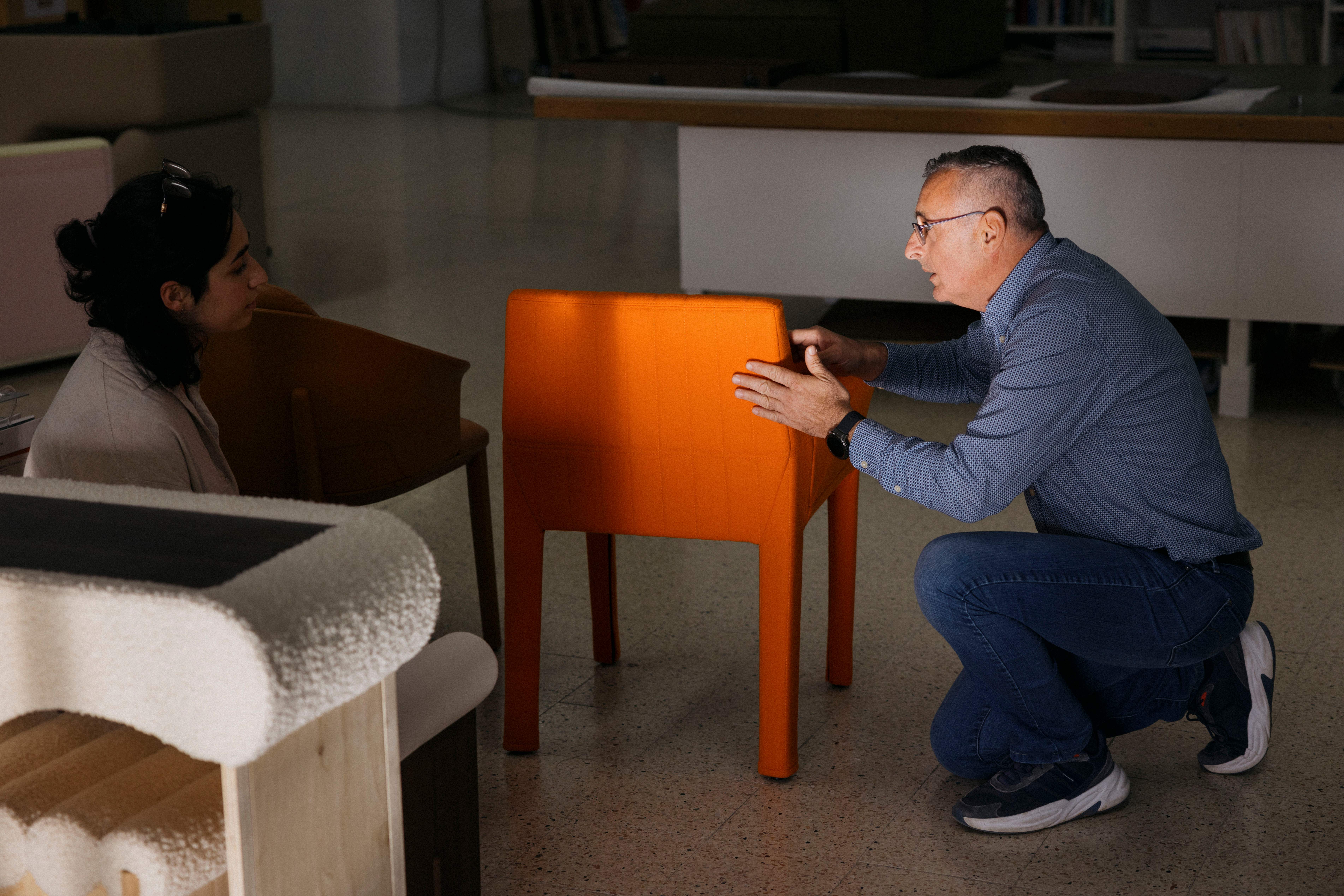
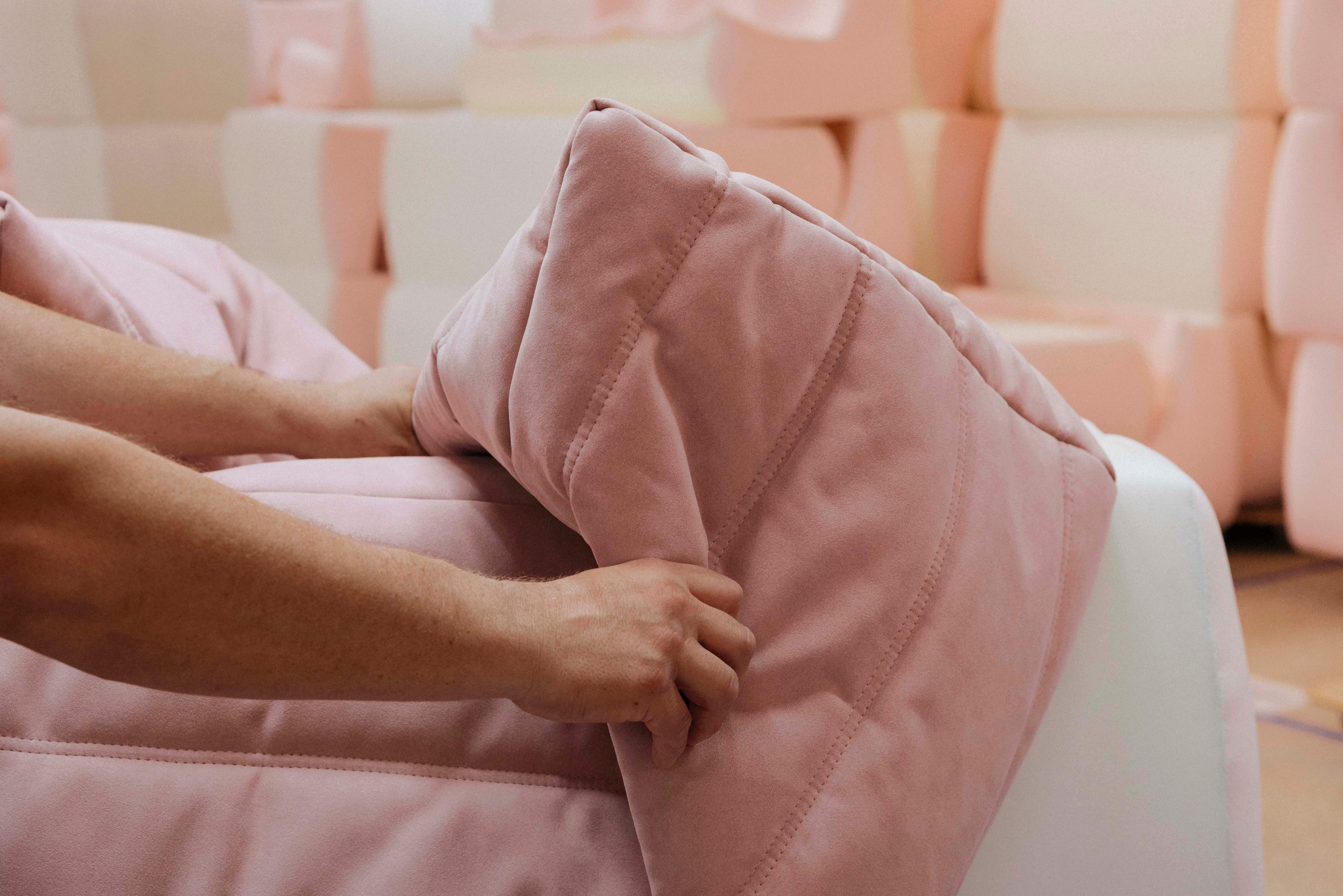
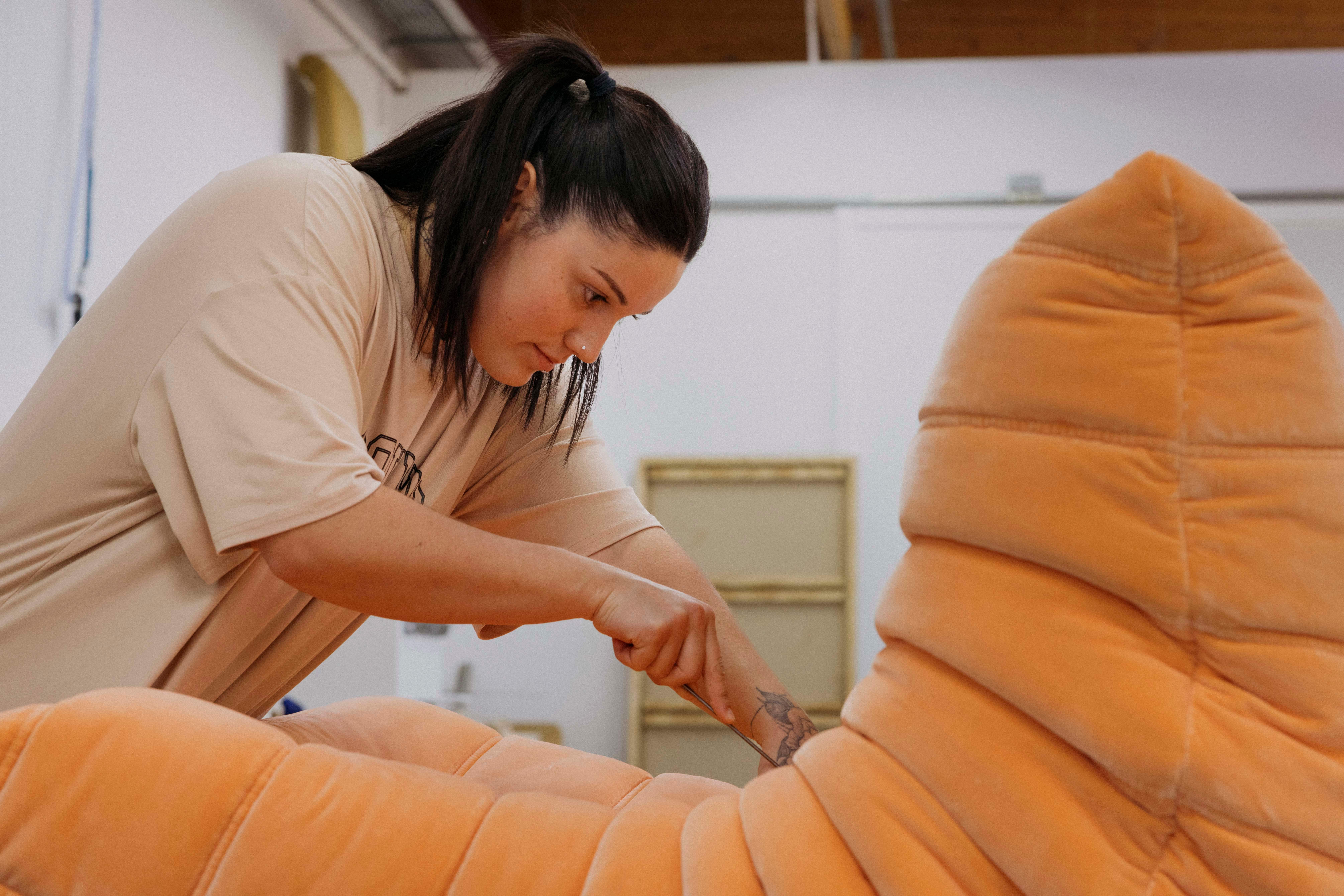
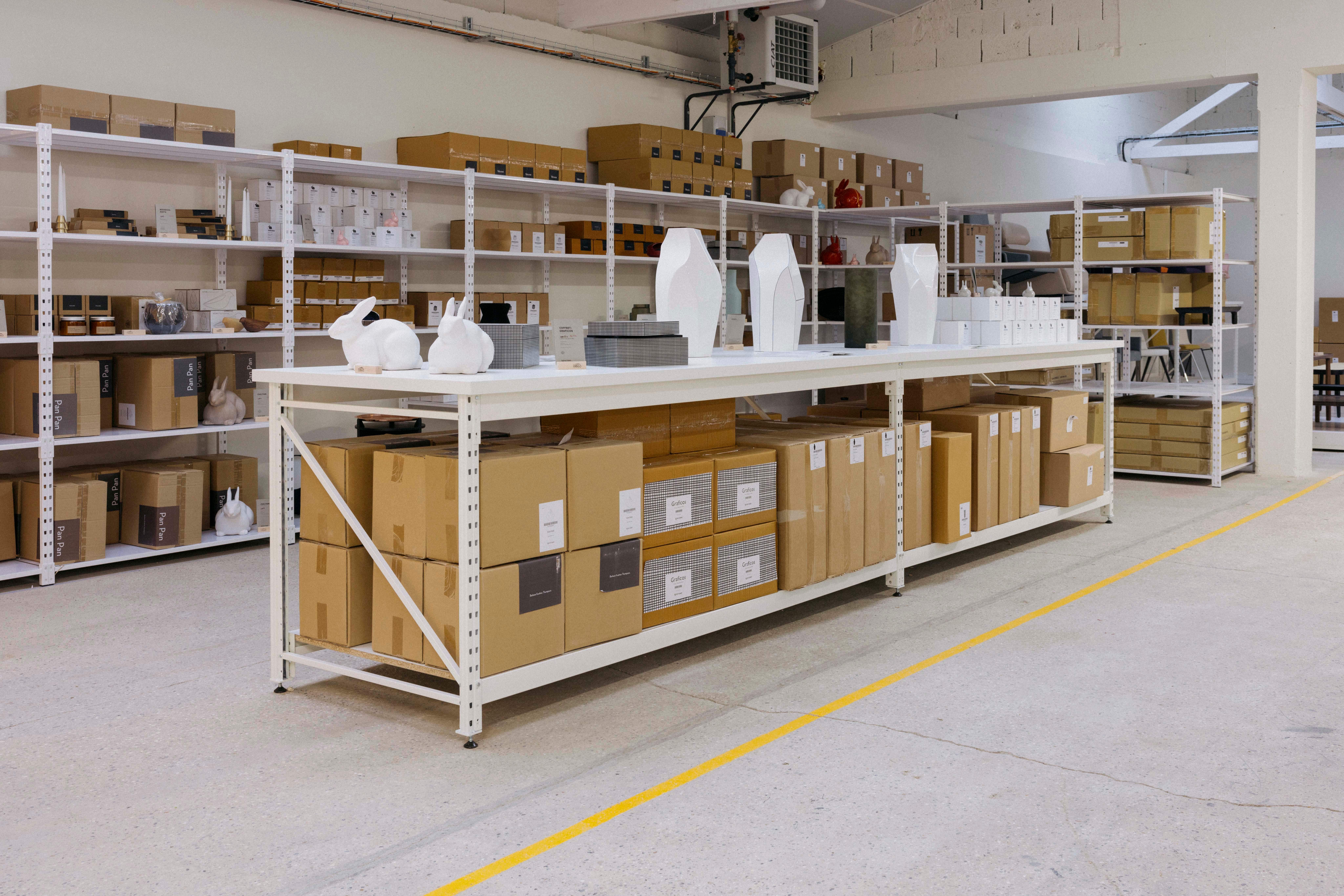
3.
footwear & leather goods
Tod’s
Bottega dei Mestieri, Italy
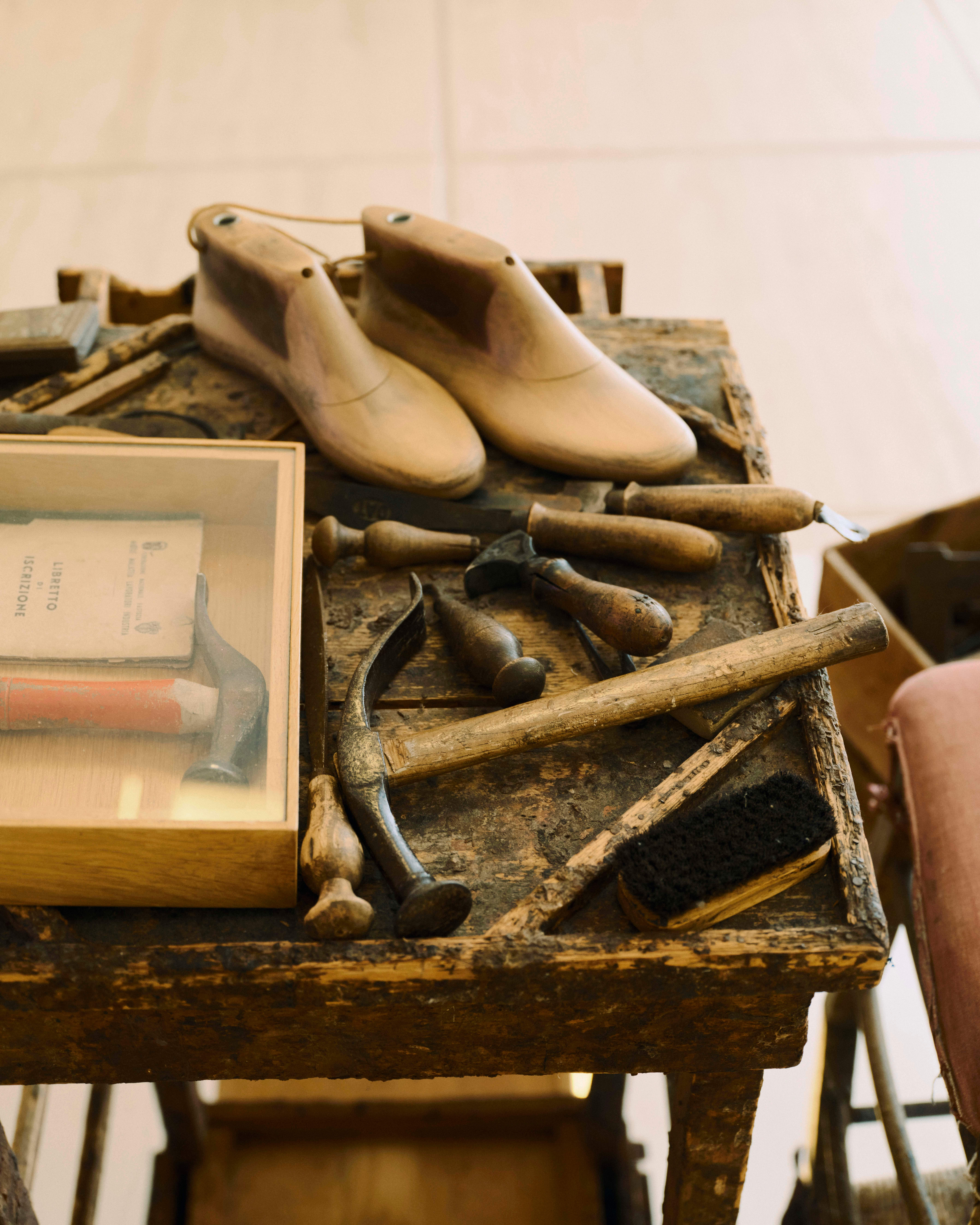
In the Brancadoro headquarters of Italian luxury house Tod’s is an old wooden worktable. It’s the table from which the brand’s founder, Filippo della Valle, started his family shoe business in the 1900s and remains a symbol of the company’s commitment to the finest handcraft.
Diego della Valle, the company’s president and ceo (and Filippo’s grandson), insists that mechanical innovation and handcraft can co-exist. He launched the Bottega dei Mestieri (“craft workshop”) in 2012, offering six-month programmes training apprentices in the skills required to make the group’s footwear, leather goods and ready-to-wear collections. Spanning three campuses, the school is run by 80 tutors; nearly 300 apprentices have graduated so far, many into jobs in the company. A walk around the factory reveals the level of precision that the students are aspiring to. While they use machines as aids, they also work with the sorts of tools that the founder used a century ago.
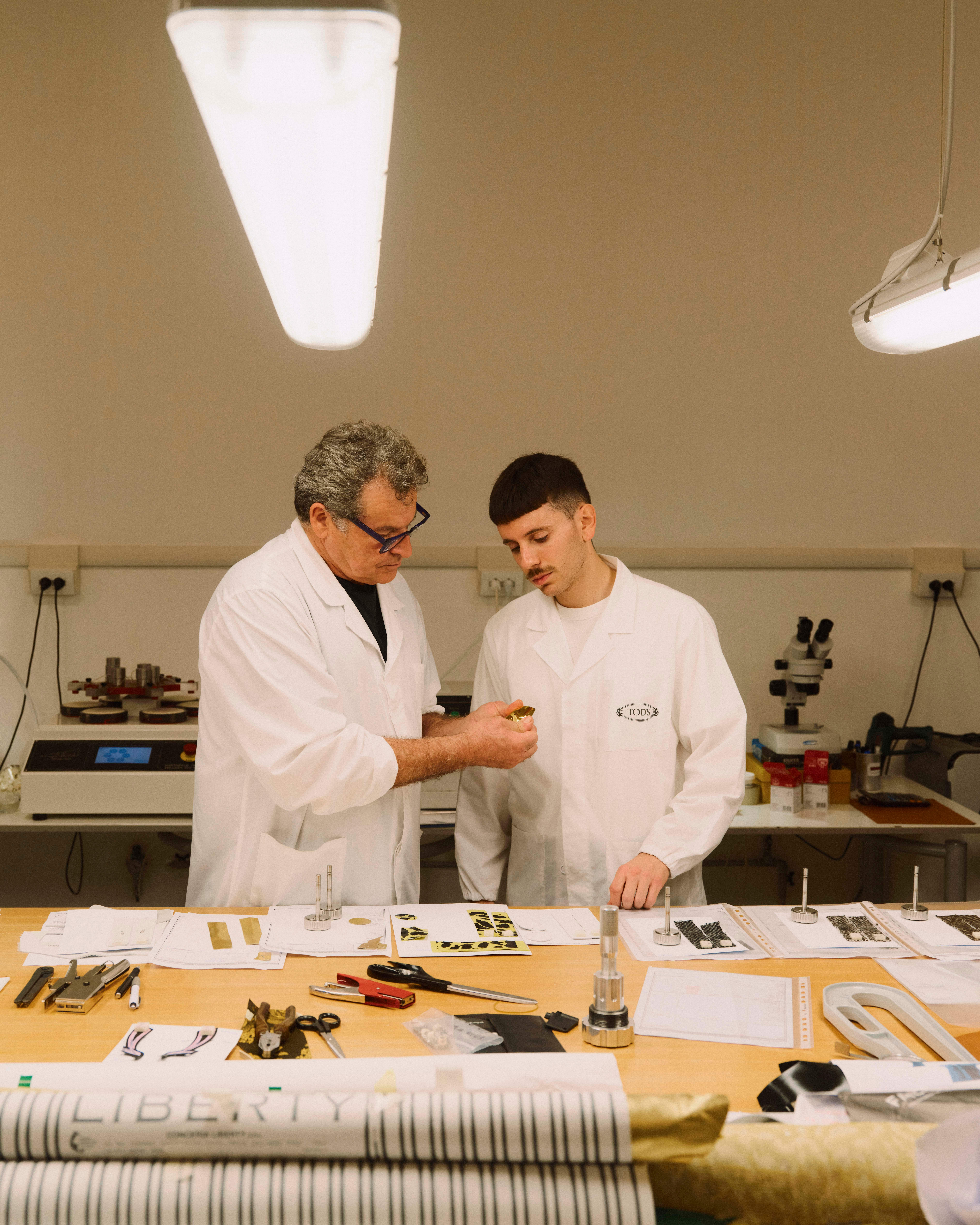
Tony Ripani is the business’s leather specialist and a mentor. “It’s touching for me to explain what I do,” says the 77-year-old Ripani, who started working for Tod’s when he was 13. “I keep at it because my goal is to teach. I have valuable experience to pass on. Otherwise, it will all disappear.”
Graduate Francesco Romagnoli is part of a new generation of artisans who see a future in a career in craft. “There was a period when artisanal work wasn’t so popular,” says Romagnoli. “Today there is more fascination with luxury and the fashion world. What has changed is that young people understand that they can be a part of something and create a truly beautiful product.”
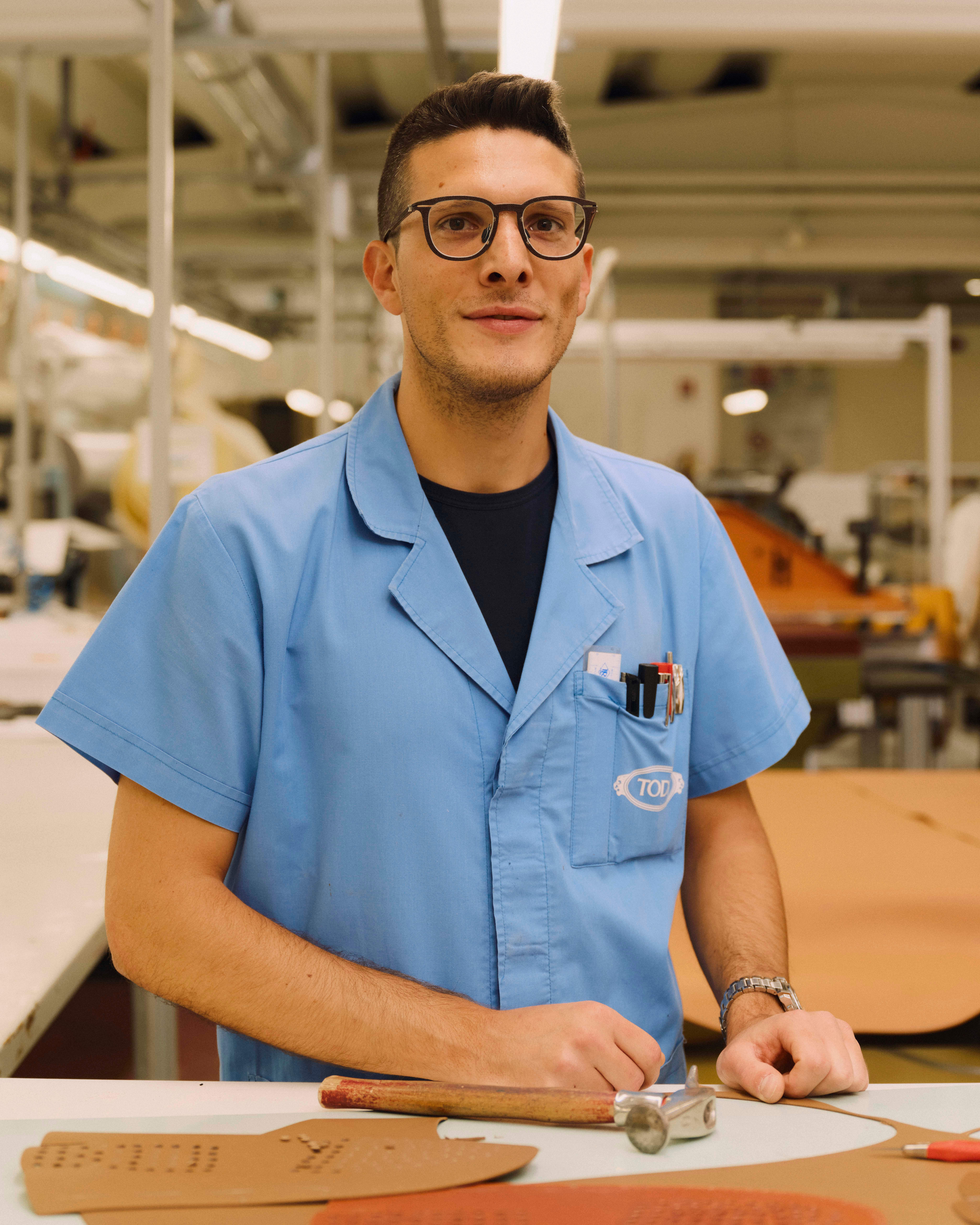
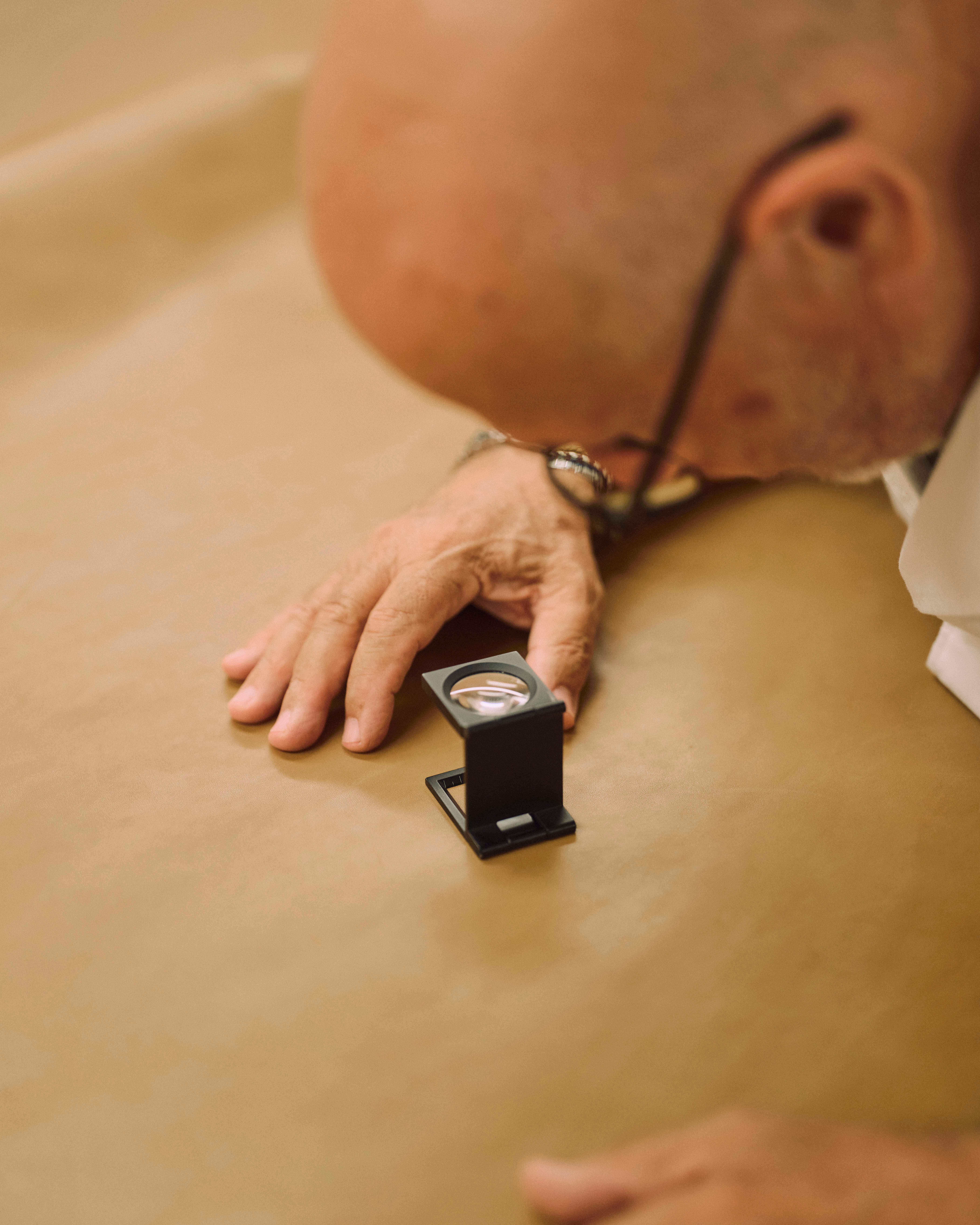
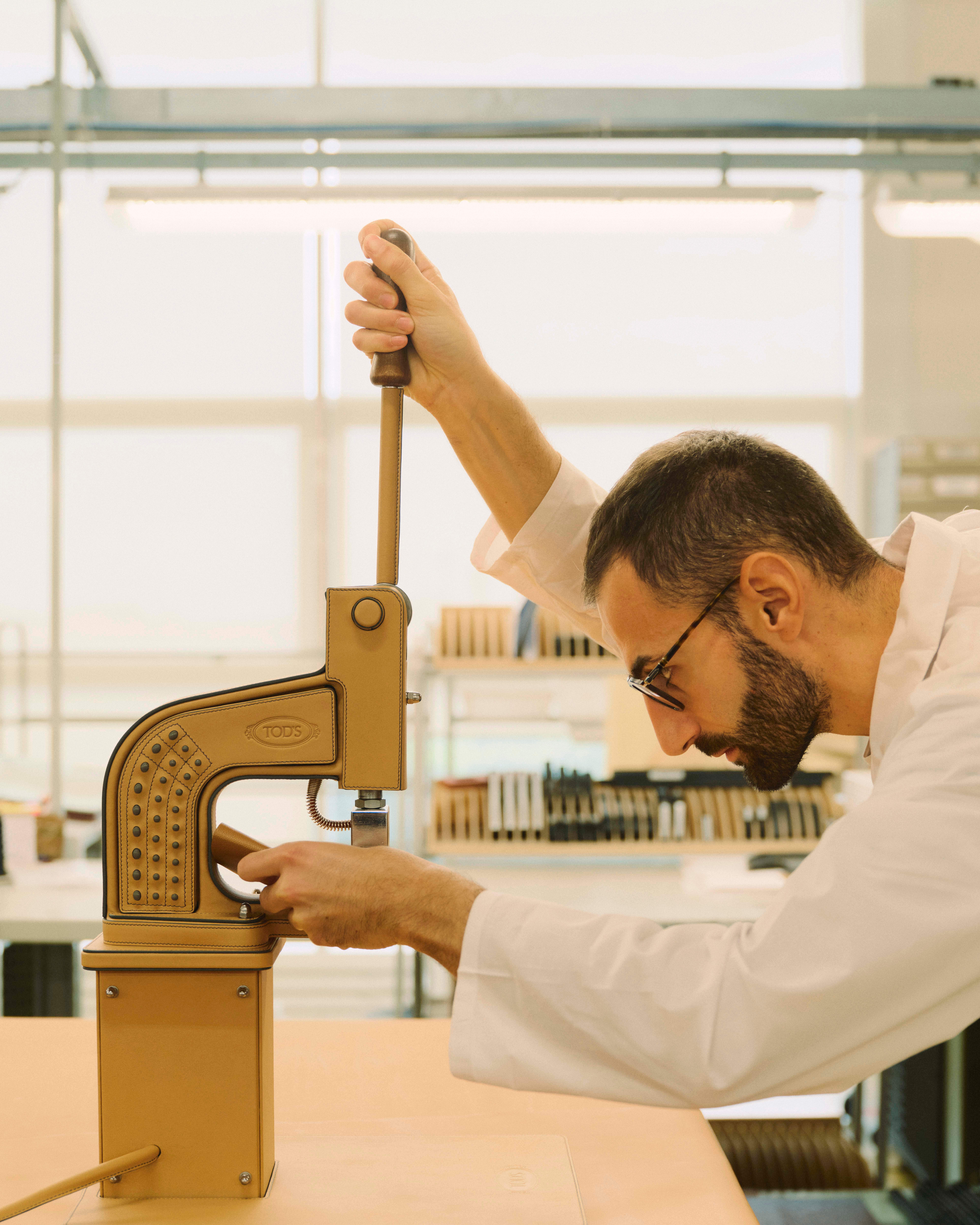
4.
goldsmithing
Buccellati
Scuola Orafa Ambrosiana, Italy
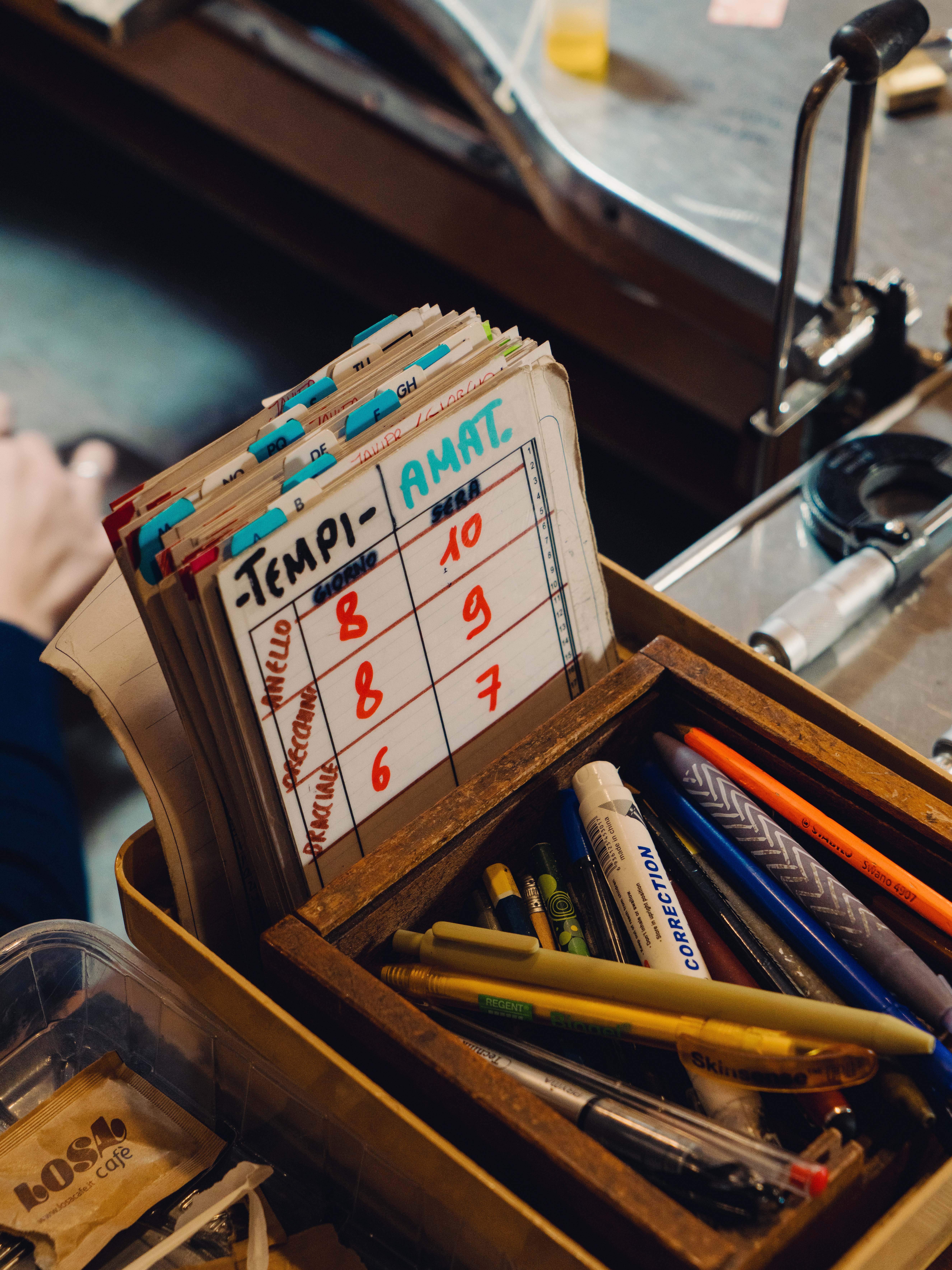
Behind a typical Milanese building in the city’s Porta Venezia neighbourhood, you’ll find one of the Italian jewellery industry’s best-kept secrets. Opened in 1995, the Scuola Orafa Ambrosiana was founded by Luca Solari to address the lack of training courses in the goldsmithing sector. “The craft was transmitted within family businesses, so it was difficult to get into if you didn’t come from that environment,” Solari tells monocle.
The school now provides an easier point of entry, with 24 courses ranging from gemmology to stone setting. Last year it introduced the Buccellati Master in Goldsmith Arts course, after years of informal collaboration with the Italian jeweller. Up to 18 students are selected; they take nine classes, each corresponding to a speciality in the Buccellati atelier. “The course aims to preserve and perpetuate techniques such as microscope stone setting, chasing and repoussé, and engraving,” says Solari. “By the end, our students become experts.” The highest achievers are offered a study grant and a full-time position in the Buccellati atelier.
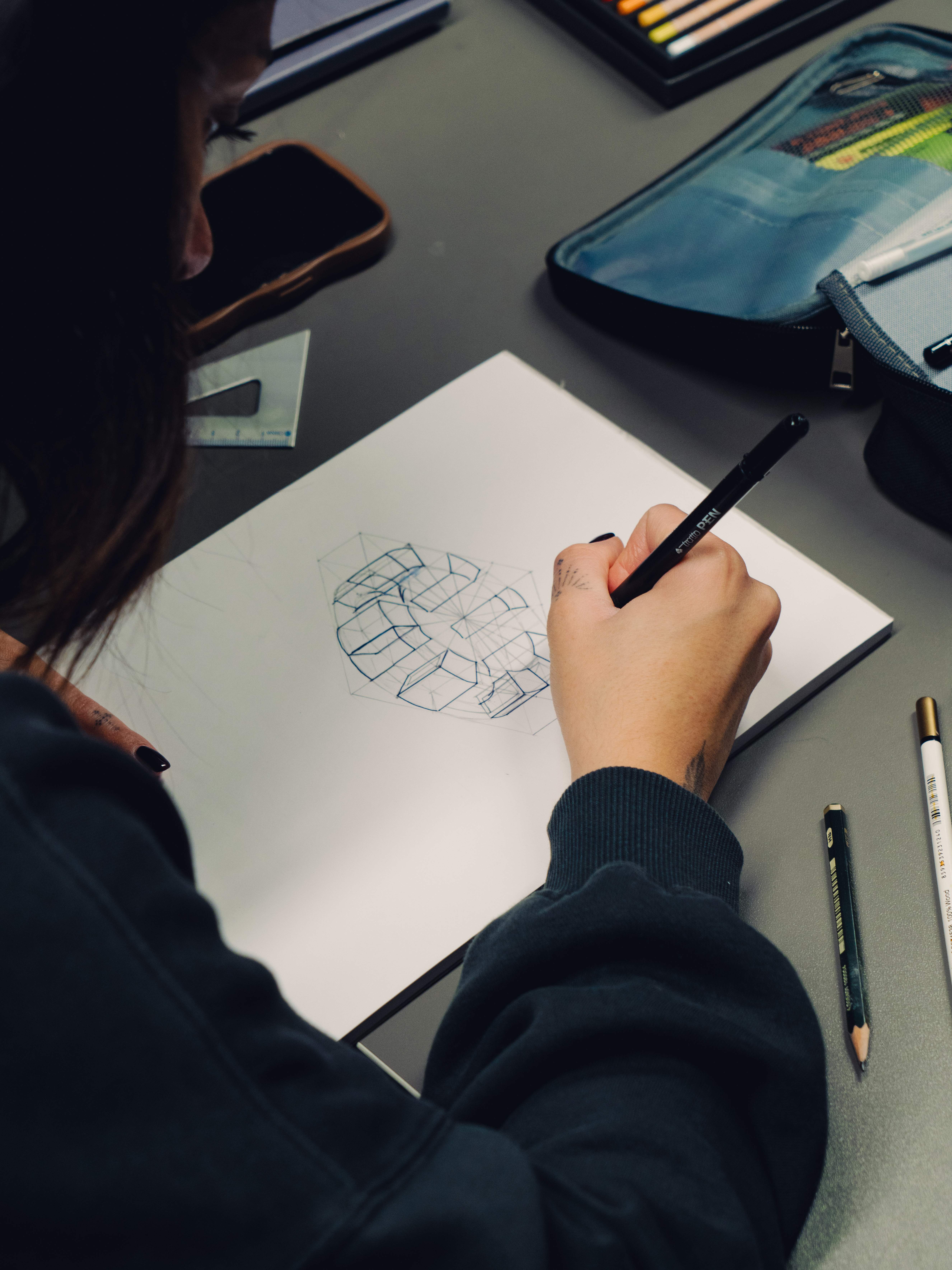
Andrea Buccellati, his family firm’s honorary president (and the grandson of its founder, Mario Buccellati), says that this partnership is designed to safeguard the brand’s future. “Investing in artisanal craftsmanship among young people is crucial,” he adds. “It’s the only way to perpetuate the Italian excellence that is admired worldwide.”
The next stage in Solari’s mission to preserve the art of goldsmithing will focus on the educators. “Training teachers is a lengthy process that’s crucial to keeping these skills alive,” he says. “We need to start discussing it now, before it’s too late.”
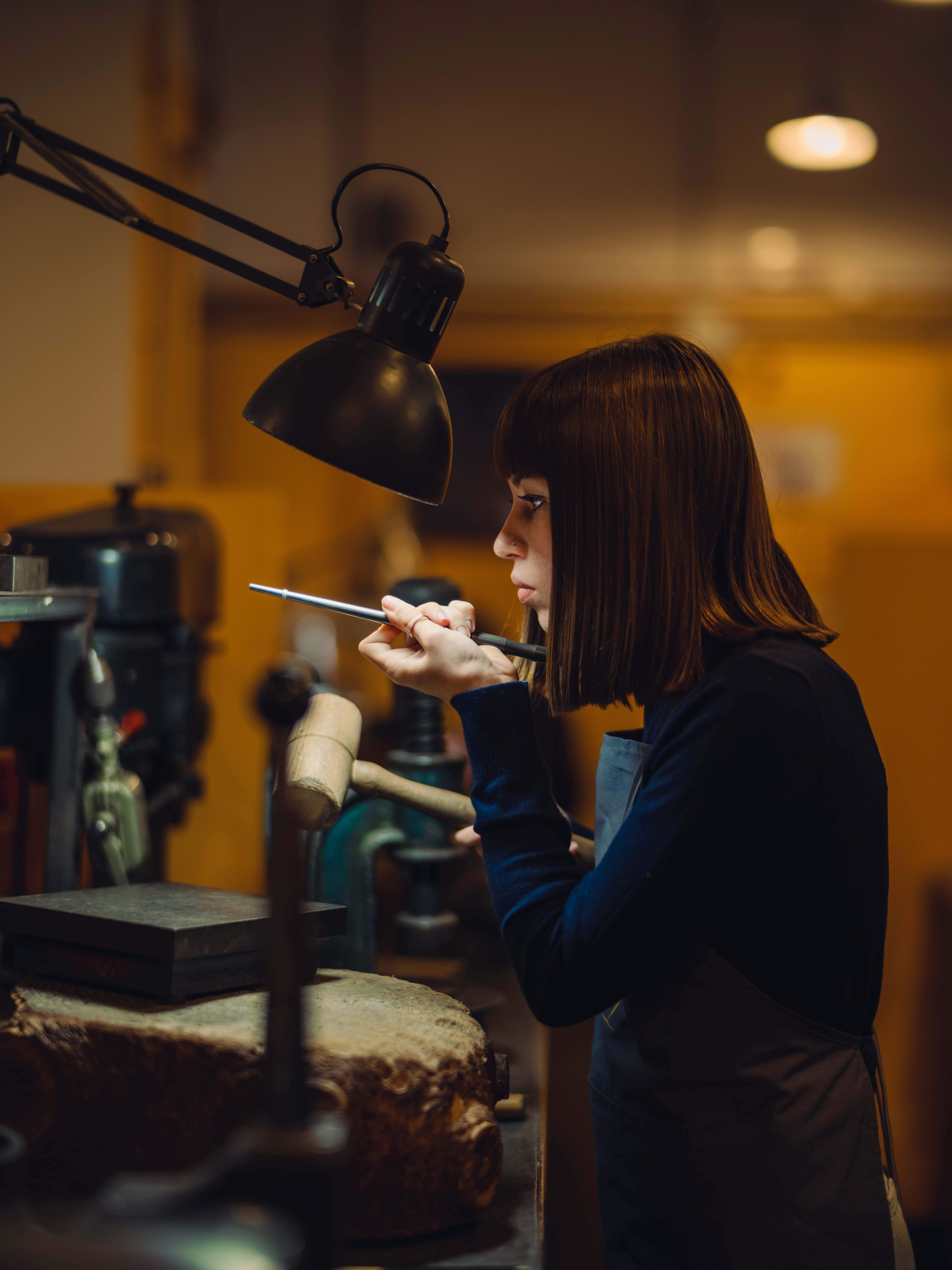
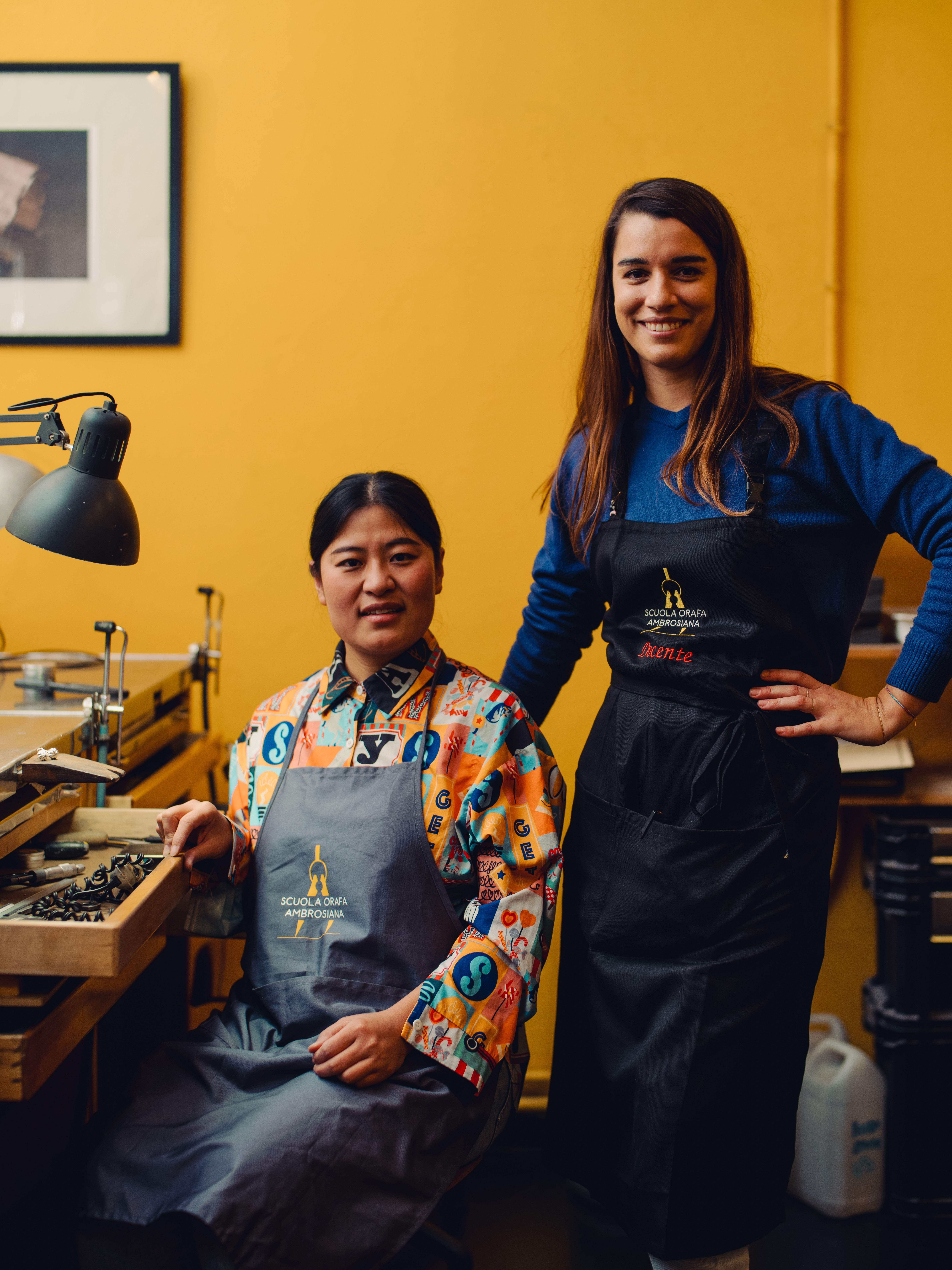
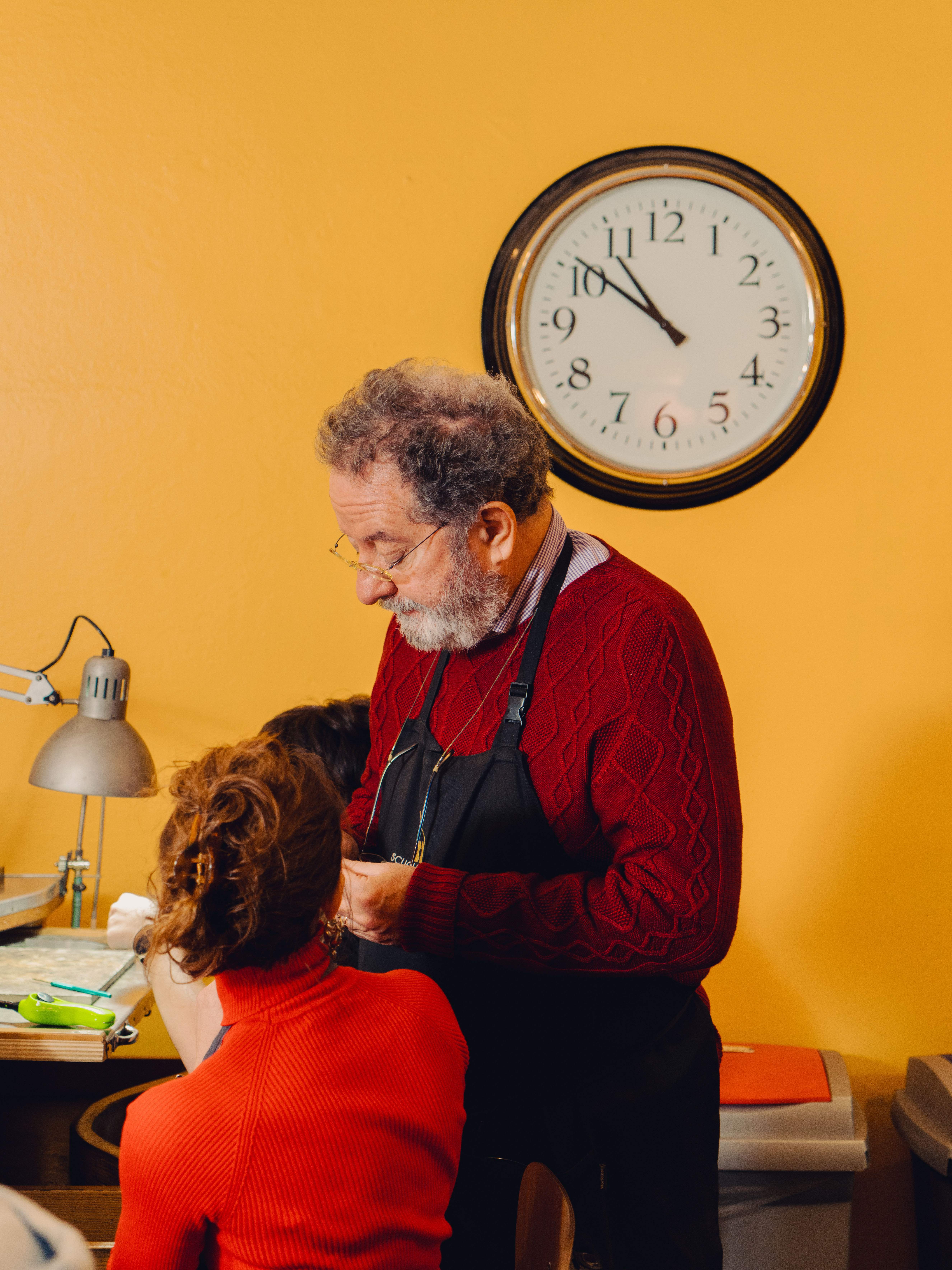

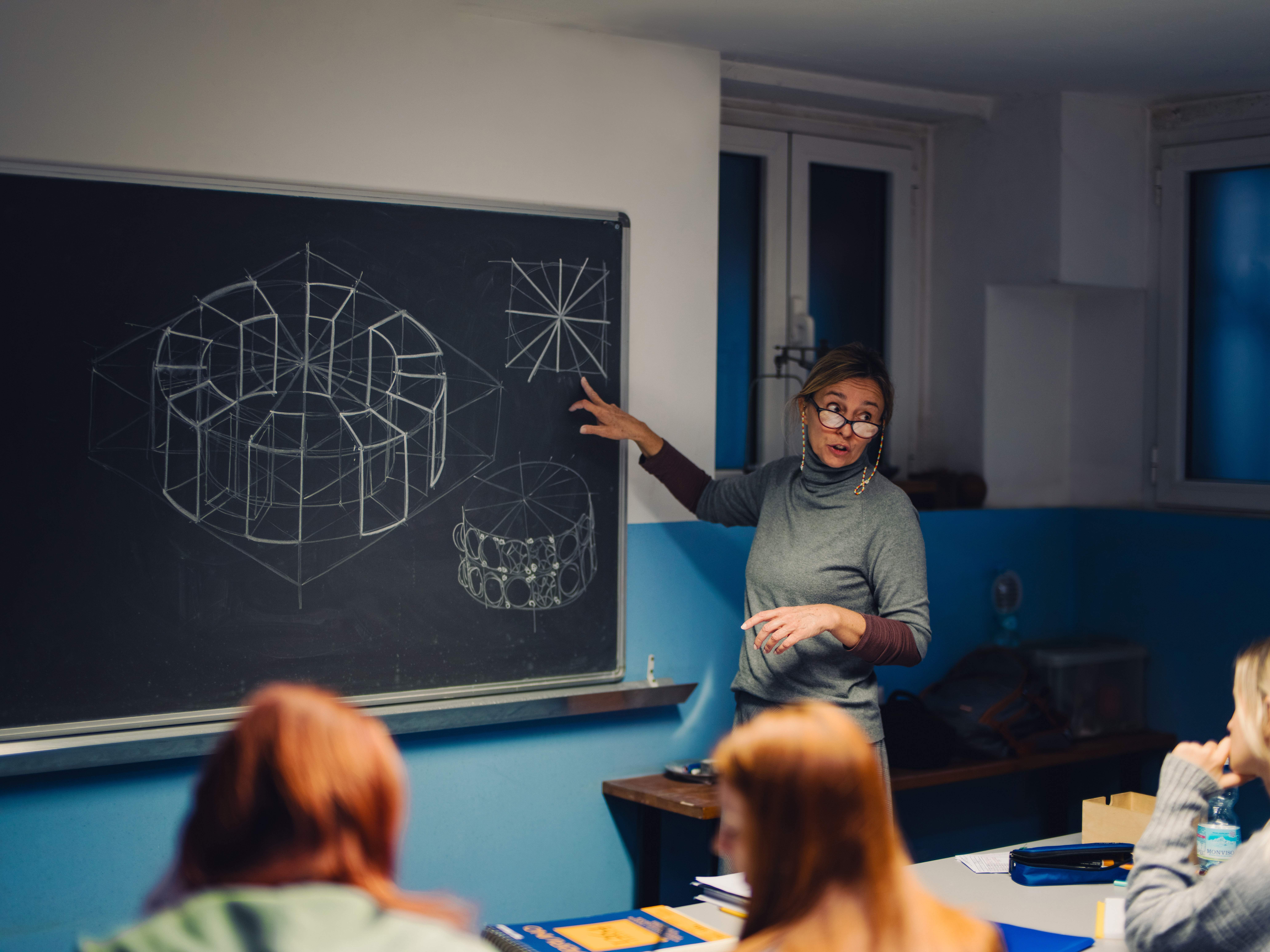
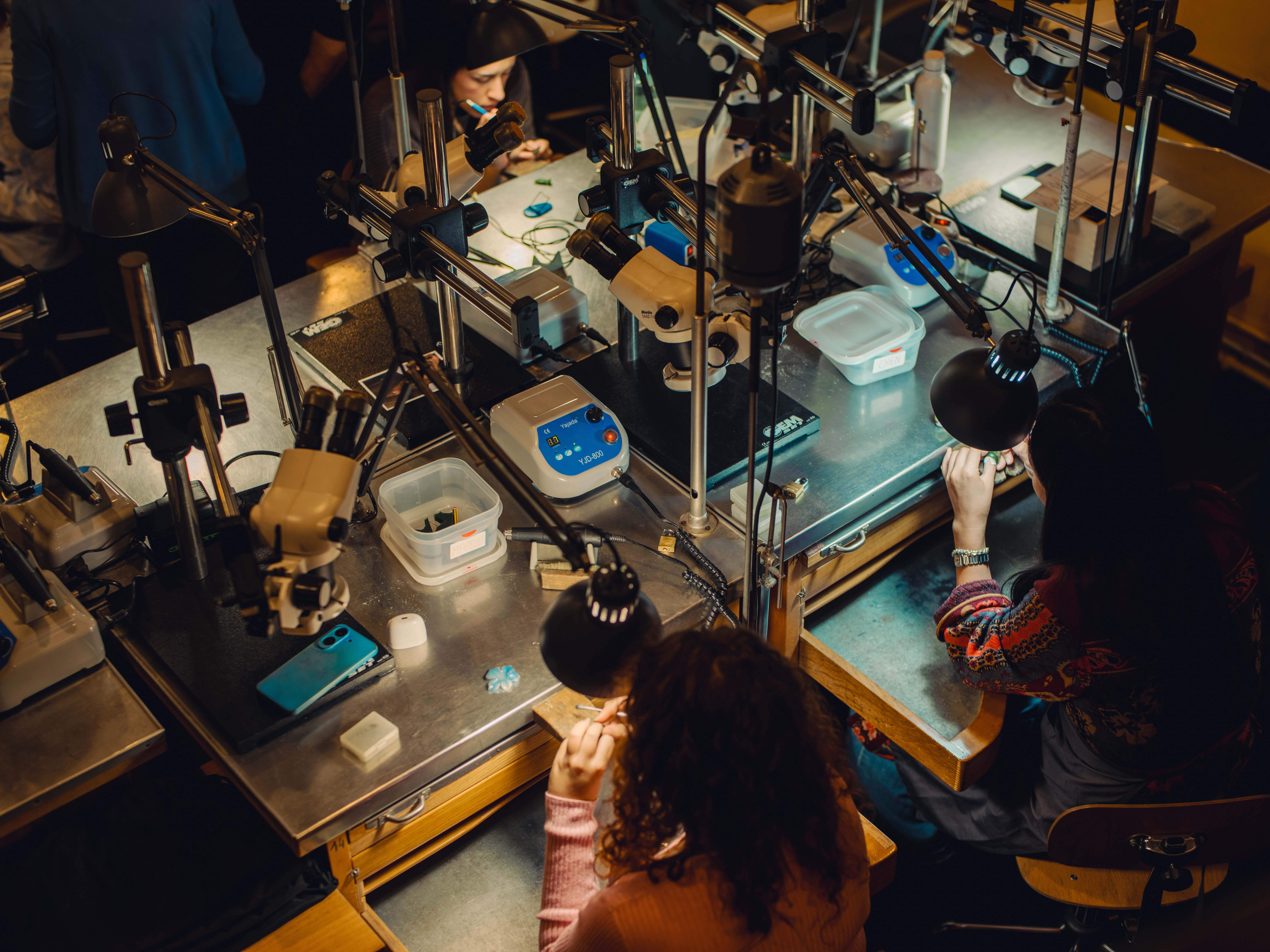
5.
timber furniture
Carl Hansen & Søn
The Lab, Denmark
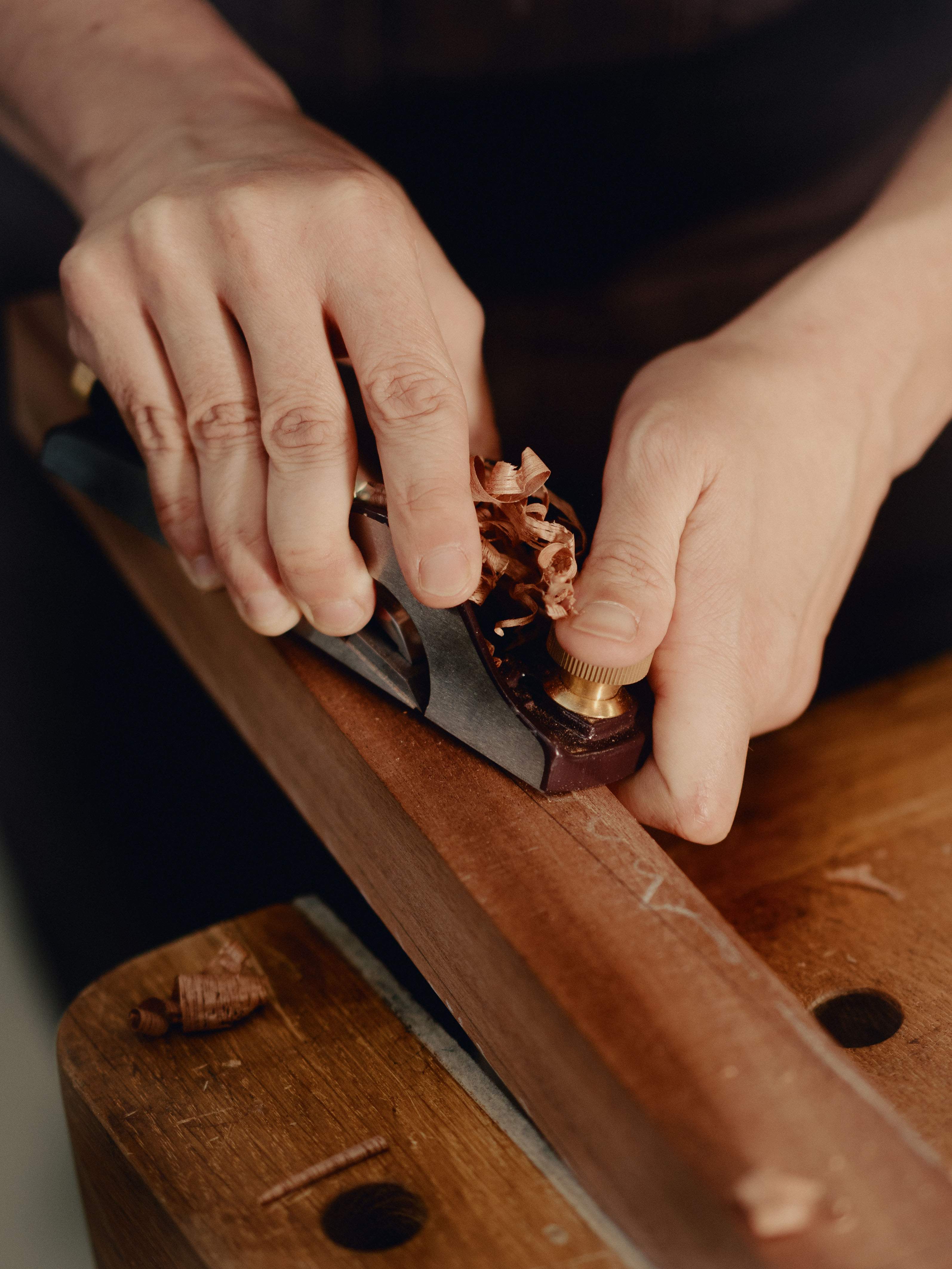
“I had been dreaming about this my whole life,” says Louise Lykkegaard, looking up from her workbench at the Carl Hansen & Søn factory in Gelsted, on the Danish island of Funen. “I had always wanted to work with natural materials and furniture of this quality. When I came here, I knew that I was in the right place.” Lykkegaard is one of 20 apprentices employed at The Lab, Carl Hansen & Søn’s in-house training workshop, founded in 2019 to preserve the uncompromising craftsmanship for which the 116-year-old, family-run company is renowned. Her dream is to one day create a new classic of Danish furniture.
Here at The Lab, apprentices don’t just learn how to restore and produce the firm’s iconic pieces, which are put together in the adjacent factory. They are also involved in reintroducing designs that have long been stored in the archives. One recent project was Kaare Klint’s English Chair from 1931, an upright rattan armchair with an ash frame. Over the course of 10 weeks, the apprentices built every piece of the chair by hand. (Lykkegaard tells monocle that she was tasked with drilling 200 holes in the chair. “That sounds boring but it was actually really satisfying.”) They also worked on Klint’s Spherical Bed, a piece defined by its distinctive curving timber frame, of which only 12 were made in the original 1938 run.

“Sometimes a black-and-white photograph is all that we have to work with,” says production supervisor Jeppe Ravn Frederiksen, who is responsible for The Lab’s apprentices. “The Spherical Bed was only designed as a single bed but they helped to turn it into a double.”
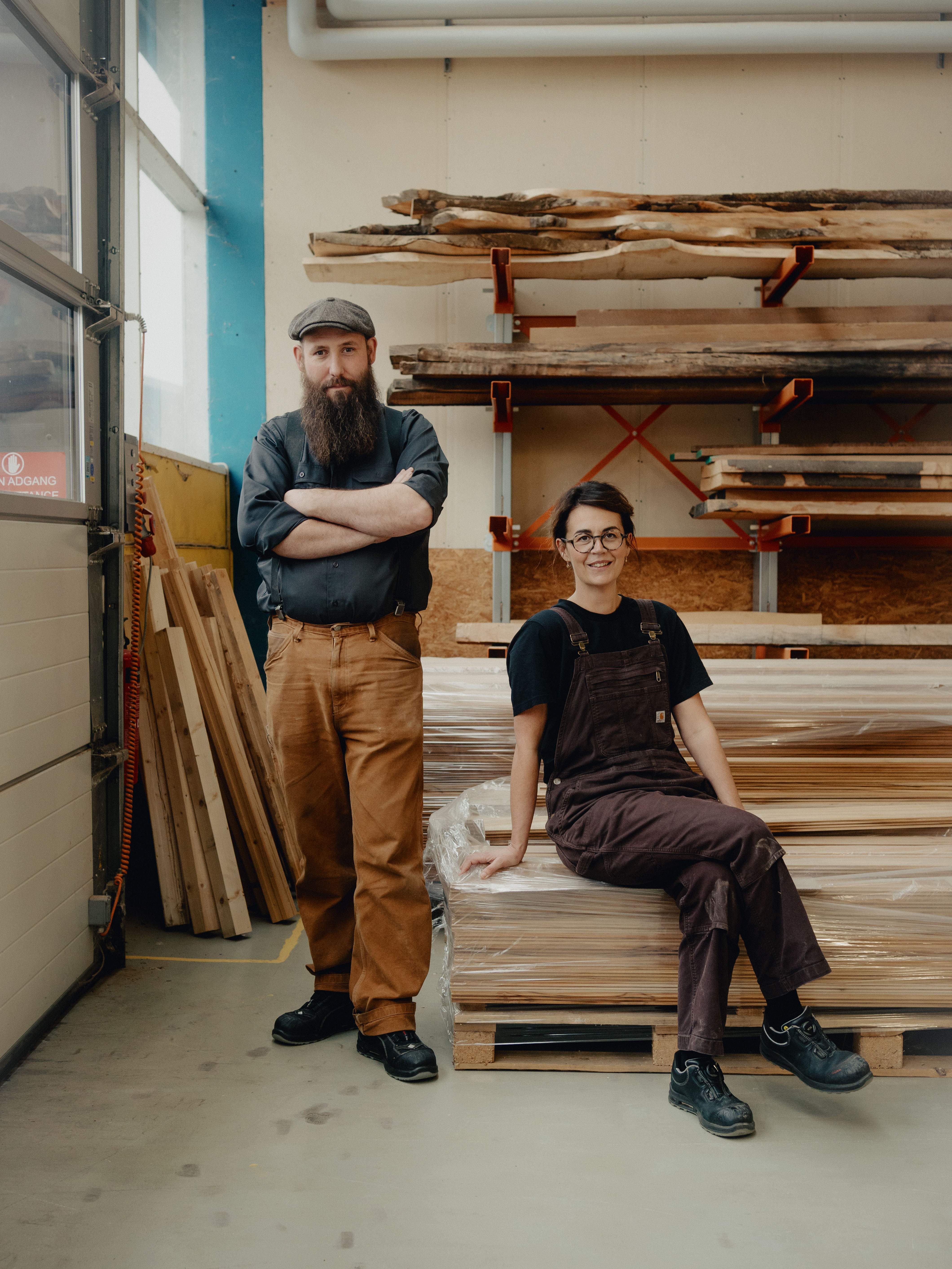
Lykkegaard is 41 years old but most of the other Carl Hansen & Søn apprentices are in their early twenties and tend to come from the western side of Denmark, where the company is based. Their day begins at 06.30 sharp; they spend three years and nine months shifting between The Lab’s technical college and the production area, with about 50 per cent of them ultimately landing full-time roles at the company.
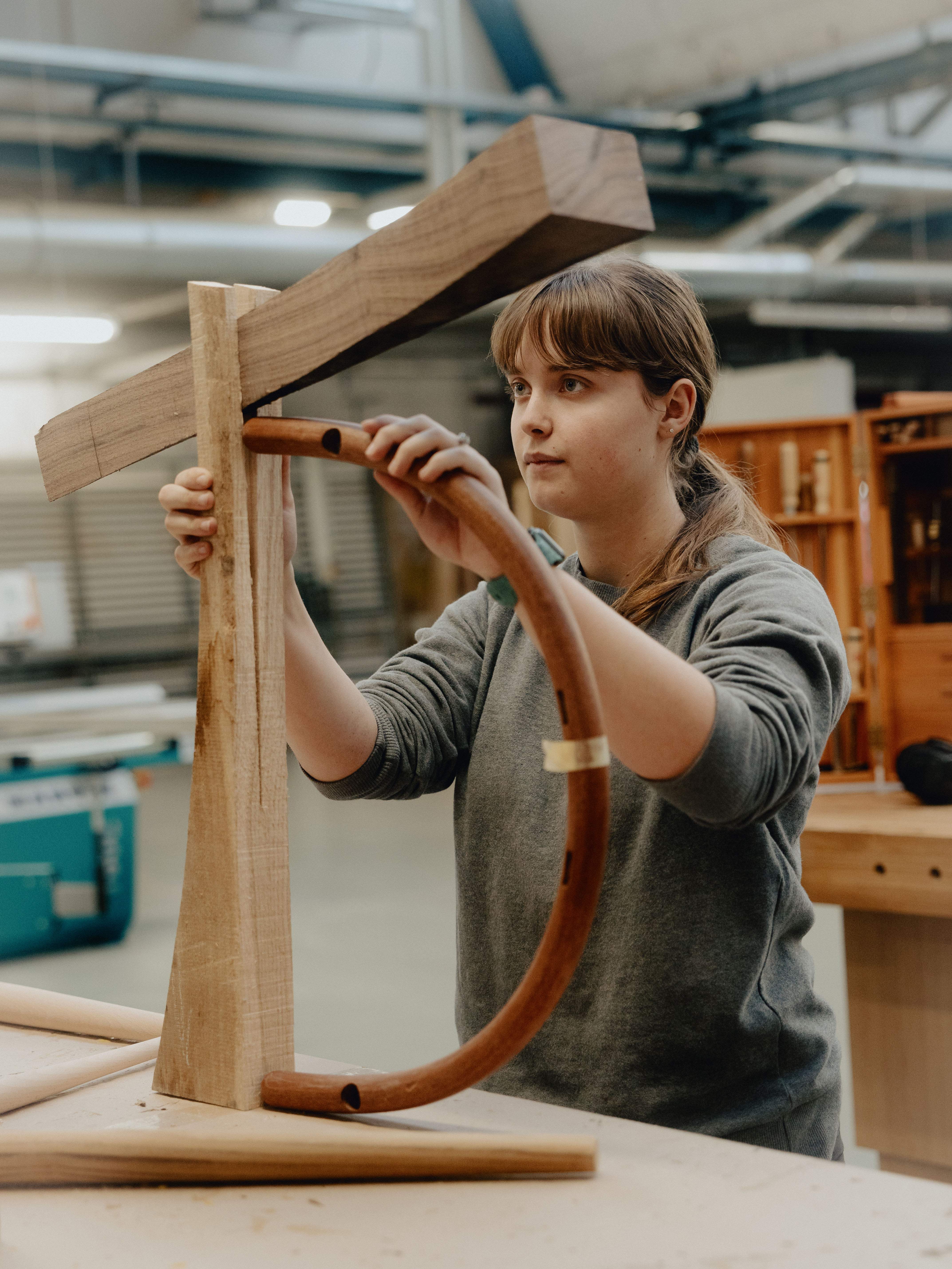
“I was at a smaller workshop before this and it was quite isolating,” says another apprentice, Chili Pedersen, who hails from the seaport town of Kolding. “This is a happier place for me. It’s really cool to make new designs. And, because of the company’s size, there’s less pressure and more time to properly learn.”
There are two types of apprentice: møbelsnedkere, trainee furniture carpenters who concentrate on hand-building pieces, and maskinsnedkere, who are taught to employ more of the larger equipment. These include the computer-numerical-control machine, which facilitates the automation of tools for use in series production.
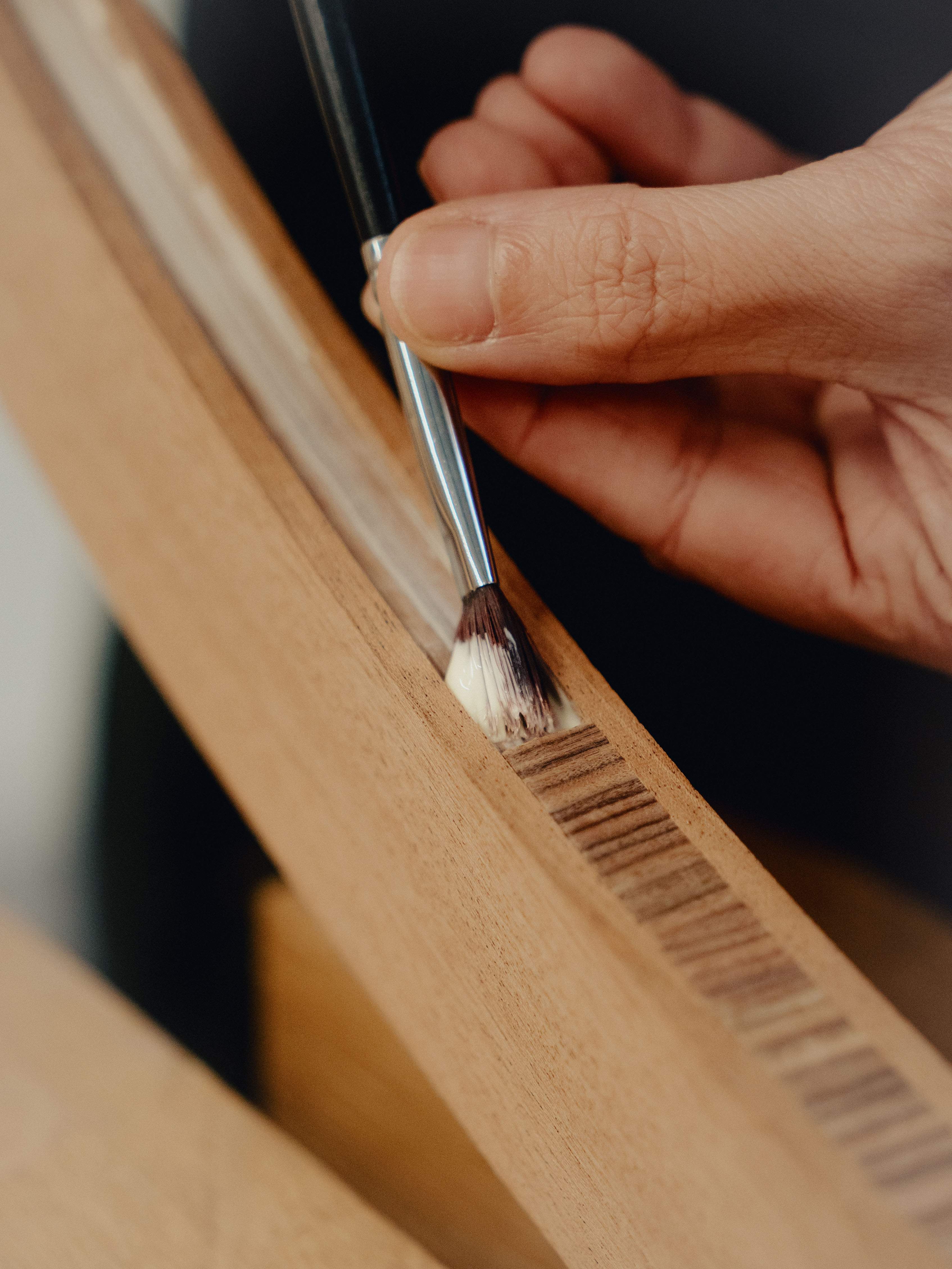
According to Ravn Frederiksen, some of the younger generation, who grew up watching online videos of craftspeople, initially find the latter aspect less appealing. “Though the handwork is where we put the love into our furniture, you still need the technical education to produce high-volume pieces,” he says. So, The Lab teaches programming and the latest 2D and 3D design techniques, and Ravn Frederiksen has been looking at ways to incorporate AI into their work. For Carl Hansen & Søn, the future supply of artisans seems assured.
Turn on, tune in: For more fresh design stories, listen to Monocle on Design on Monocle Radio. Plus, stay up to speed, stay on point and ensure that you’re always in style with our new programme, Monocle on Fashion.