Observation: Olympic bikes / Berlin
On the fast track
What makes German athletes go faster? Bikes made by a Cold War-era company. Can we ride one of their €70,000 inventions? Er, no.
Aspiring engineers in Germany typically do not have a hard time landing well-paid jobs. After graduating, almost all of Orfeo Nil’s classmates headed to Stuttgart or Munich for well-cushioned careers in the car industry. For his internship, however, the Brazilian-born 27-year-old sought out a nondescript workshop in Schöneweide, southeast Berlin. When he meets monocle, he is wearing protective glasses and polishing a black carbon-fibre disc. The component will become the wheel of one of the world’s fastest track bicycles. “There’s no other bike like the ones made at fes,” he says.
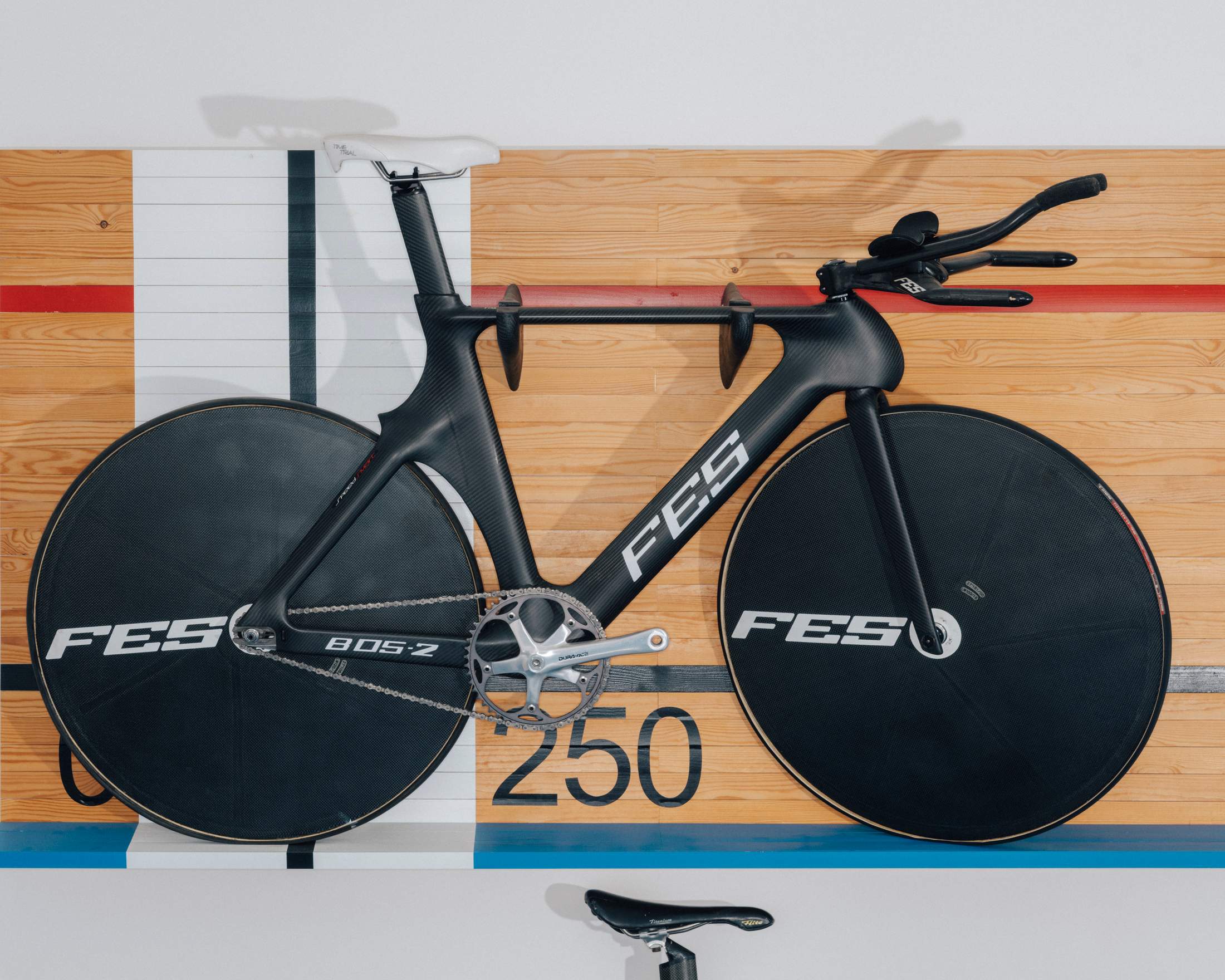
Ready to ride
fes is short for Institut für Forschung und Entwicklung von Sportgeräten, the state-funded organisation that propels Germany’s athletes to victory. The institute produces kit used by Olympians across 14 sports, including most that Germany excels in: cycling, rowing and canoeing in the Summer Games; luge, bobsleigh and skeleton in winter. Though this year’s Olympics were disappointing for Germany, fes was involved in almost a third of the country’s medals. In the 2022 Winter Games, its share was more than 75 per cent.
With a staff of 90 – mostly lean Germans with aerodynamic buzz cuts – everything is manufactured from start to finish across fes’s three floors, which contain offices as well as carbon-fibre and steel workshops. “We cover so many sports, with everything under one roof,” says director Michael Nitsch. “I don’t think there is anything comparable in the world.”
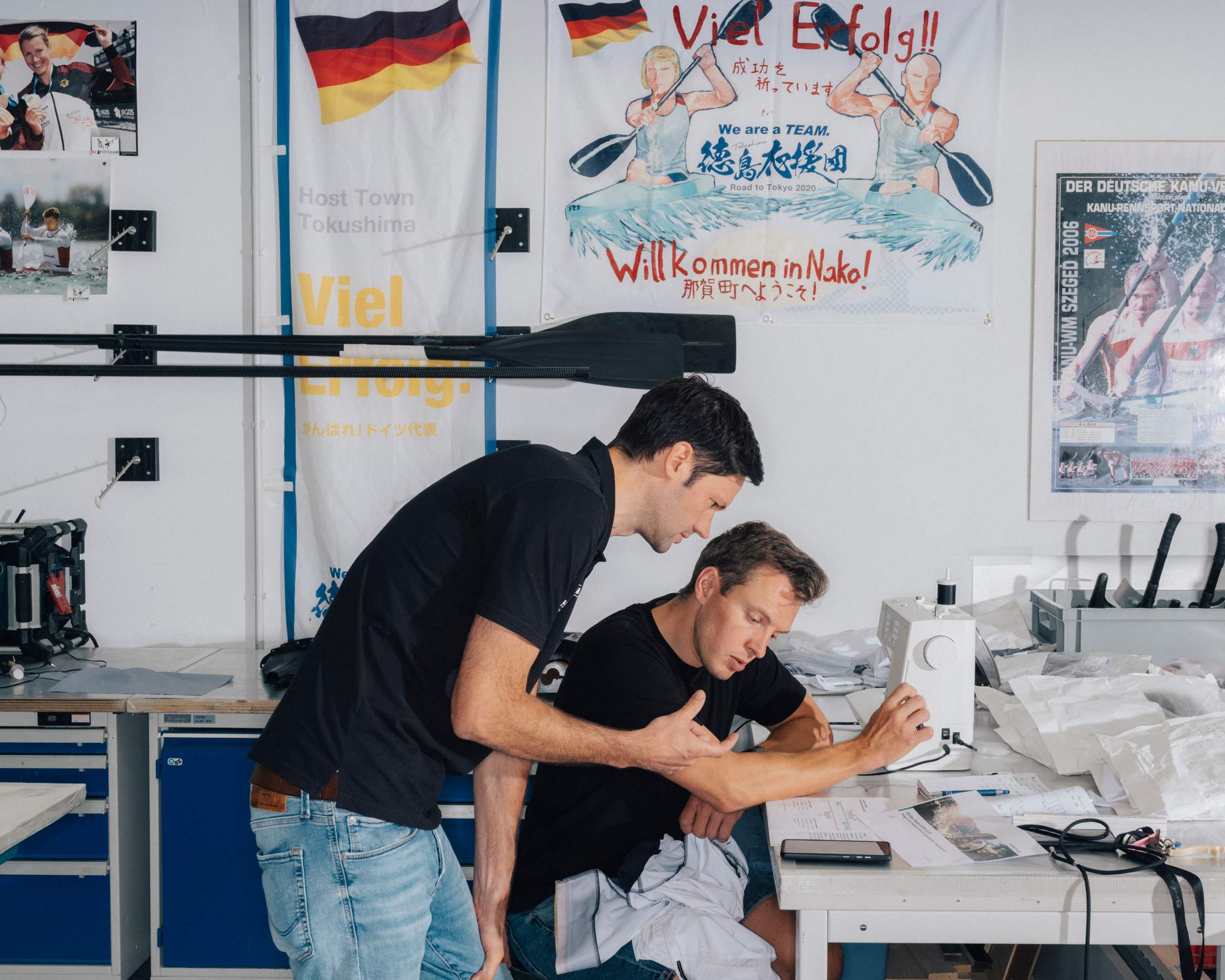
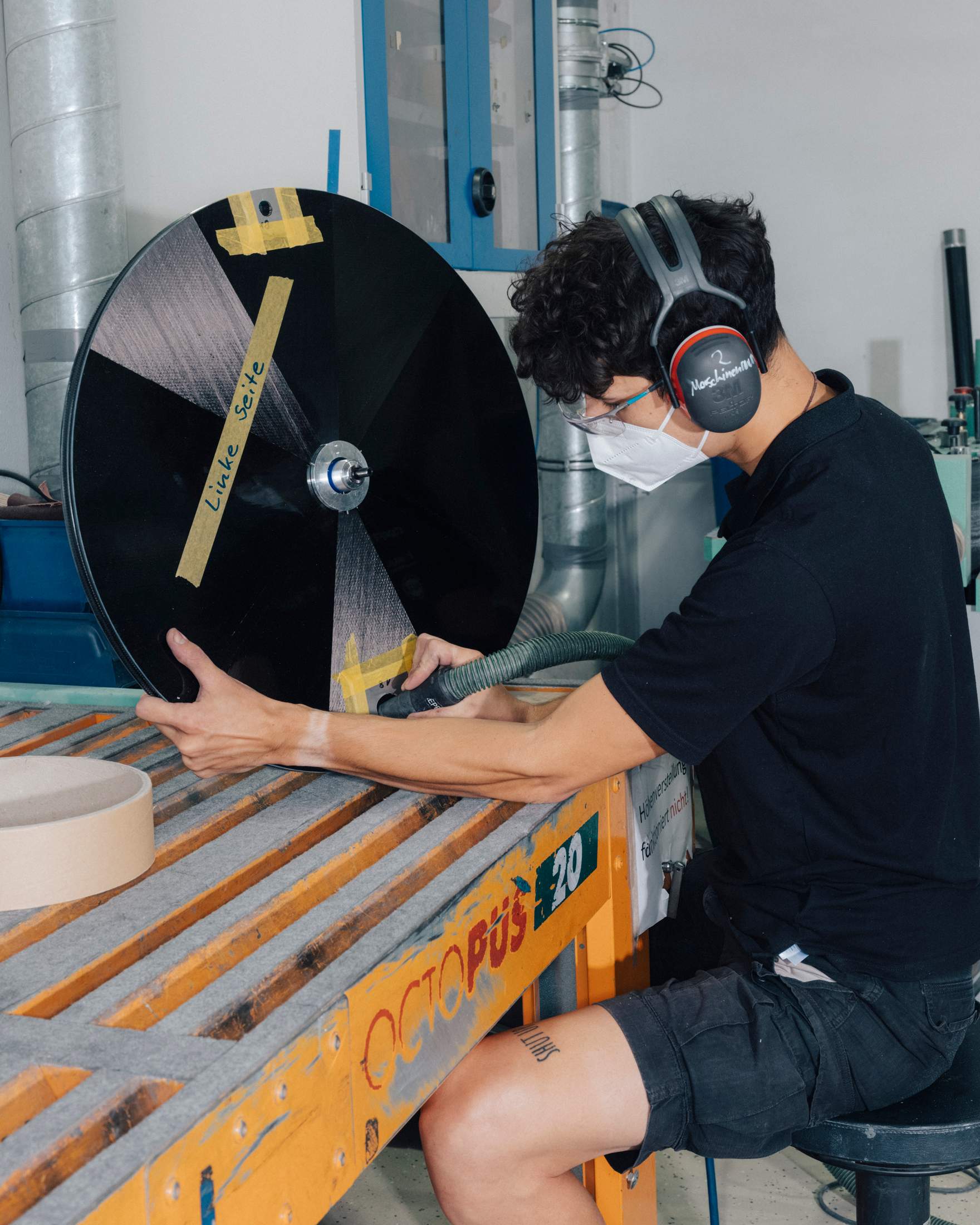
fes was founded in 1963, when this part of Berlin was inside the gdr. With the Cold War as a motivator, East and West Germany were often racing helmet to helmet in Olympic velodromes. Many of fes’s bicycle innovations were quickly adopted across the Iron Curtain, including making frames from carbon fibre and switching from spokes to disc wheels. Preserved post-reunification, the institute works with a modest budget – about €10m in 2024. Only a few firms can rival the wheels moulded at fes. “Regulators often look for features that only fes have and ban them,” says Nitsch. “We take it as a compliment.”
At the workshops, the manufacturing process begins with the frame, made almost entirely from carbon fibre. It arrives pre-mixed with glue and rolled up like a textile, before being cut, moulded and baked into shape. “You have three things to think about: the feet, the hands and the ass,” says Nitsch. “The secret is how you position these things.” But this humility is partly obfuscation. The b20, fes’s latest model used at the Paris Games, is made from more than 500 components – all individually engineered and moulded in-house. The improvements included a tweaked fork (the bit that connects the wheel to the frame) and a carbon-fibre crank (the part that the chains bolt onto). “At this level, the improvements are tiny tweaks,” says Nitsch. “Everything counts.”
When monocle asks whether we can take a bicycle out for a spin, Nitsch looks appalled. “We don’t even let these bikes roll on normal floors,” he says. “It makes no sense.” Only professional athletes – as well as the occasional lucky intern – are welcomed into the fes velodrome. Still, there is hope. Olympic regulations stipulate that all gear used by athletes must be commercially available, so fes bikes are for sale. These Weltspitze wheels could yet be ours – for a mere €70,000. —